Introduction
A typical refinery gets its crude supply from various sources that vary greatly in properties such as density, sulfur content, and volatility, and consequently, vary the feed quality to the crude unit. Ideally, the crude distillation unit in the refinery needs to be optimized online for yield and cut quality for product blending and other product slates for every crude feed, but may cause variation in the tower operational parameters and may not be desirable. Alternatively, crudes from various sources may be blended upstream to produce a uniform feed to the crude unit.
Objectives
The implementation of crude blending control and its integration with other sub-systems can achieve the following objectives.
- To minimize the dependency on the source for the crude feed properties and thus stabilize and optimize the operation of the crude unit.
- To maximize the side-stream yields and optimize targeted side stream qualities for product blending.
- To improve crude oil inventory for just-in-time manufacturing.
- To reduce demurrage cost by better planning and scheduling of the crude unloading operations.
System integration
The benefits of crude blending by itself can not be realized unless it is integrated with other sub-systems for optimization, operational stability, and just-in-time manufacturing. These sub-systems can be categorized into two areas, namely, modules for crude quality control integration and modules for product quality control integration.
Crude quality control sub-systems
The crude quality control sub-systems and their roles in integration are as follows:
No. | Crude Quality Control Modules | Purpose |
I | Marine Planning and Scheduling | To interface with ships’ arrival schedules and plan a strategy for unloading of crude into crude tanks based on the refinery operational targets. |
II. | Movement Task Monitor and Control | To automate the crude unloading operation into crude tanks based on the strategy planned by Module-I. This module is mainly responsible for Oil Movement and Control (OM&S) functions. |
III. | Crude Tank Composition Monitoring, Control, and Optimize | To compute the composition and properties of each crude tank for current tank contents. This module also computes the optimum crude mix recipe for each tank based on planned crude unloading and short-term refinery run plans for the crude units. |
The above sub-systems are integrated only for the quality control of feed to the crude distillation unit and do not account for the optimum operation of the crude distillation unit and product blending optimization. Implementation of only crude quality control modules would require the targeted properties of the feed to the crude unit as manual input to module-III described above. Thus they would achieve only part of the benefits of overall integration of both crude quality control and product quality control modules.
For example, target crude feed composition would depend upon the product blend optimization and target qualities of the side-streams of the crude unit. Feedback from the product quality control modules not only would compute the targeted crude feed composition but also set the targets for optimum operation of the crude unit.
Product quality control sub-systems
The product quality control sub-systems and their roles in the overall integration and feedback to the crude quality control sub-systems are as follows:
No. | Product Quality Control Sub-System | Purpose |
IV. | Crude Unit Model | To feedback the target crude feed properties to the crude quality control module-III to optimize the crude mix recipe for the crude unit. This module also set the target for the operations of the crude unit distillation unit for module II described below. This module closes the loop and integrates both product quality control and crude quality control modules. |
V. | Crude Unit LP Optimizer | To optimize the operation of the crude unit based on the target side-stream qualities and draw-off rate. This module uses model-based control using the LP algorithm. |
VI. | Product Blending LP Optimizer | To optimize the recipe for product blending based on product specs, component qualities, availability, and other constraints. This module uses the feedback from an online blend header analyzer to adjust the setpoints of component flow rates. Tank quality integration adjusts online the target specs for the product tank during blending |
Figure-1 shows a graphical representation of crude quality control and product quality control sub-systems for an integrated crude blending, scheduling, and optimizing system.
The functionality of the application modules
There are the following four functional modules of the crude blending sub-system that are either custom developed and/or integrated with other software available from third-party vendors.
- Crude Planning and Scheduling
- Crude Tanks Quality Control (Ship to Tanks Blending)
- Crude Tank Composition and Inventory Monitoring
- Crude Feed Quality Control (Tanks to Crude Units Blending)
Figure-2 shows the interrelation and information flow of the modules mentioned above. The concepts of these application modules are discussed briefly in the following sections to give the reader some ideas about the complexity of crude blending application modules.
Crude planning and scheduling
The purpose of this application module is to plan and schedule (for at least 1 to 2 months in advance) the unloading of crude from ships into various crude tanks. This module interfaces with the refinery’s existing or planned computer application for crude ships’ schedules, types, and amounts of crude, third-party software for planning and scheduling, and a module for the monitoring of crude compositions and properties in the crude tanks. This module requires input information in terms of schedule for target operation parameters such as crude feed density, types of crude and crude unit side streams flows and would generate output for unloading schedule for each ship crude and OM&S tasks for blending of crude from ship to crude tanks.
Figure-3 shows the flow of information and interaction among various applications for the crude planning and scheduling module.
Crude tanks quality control (ship-to-tanks blending)
The purpose of this application module is to execute the OM&S crude blending task as optimized by the planning and scheduling module and initiated by the task control module of the OM&S automation module. This application is merely a ratio control application to start and stop the unloading activities when the exact amount of a given crude is unloaded into the designated crude tanks.
- Interface: The application will interface with the crude tanks monitoring module for the online updating of the composition and properties of crude in the blended crude tanks.
- Input: Since the application will have all the required information for the blend, it would not require any additional information from the operator except for scheduling the blend OM&S task.
- Output: The application module will generate only necessary “End of Blend” reports and updated the crude tank’s composition as retrieved from the crude composition monitoring module
- Information Flow: Figure-4 shows the flow of information for the crude blend from ship to tank module.
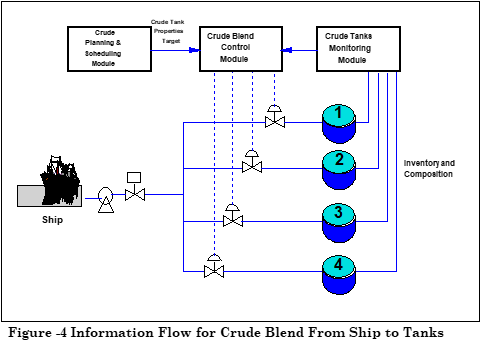
Crude tank composition and inventory monitoring
The purpose of this application module is to monitor the composition and inventory of each crude tank for both loadings (from ship to tank) and unloading (from tank to units) operations.
- Interface’s: The application will interface with the tank gauging system for the crude tanks and application module for the blend of crude from ship to tanks to keep a track of incoming amount and type of crude.
- Input: Since the application will have all the required information for the blend, it would not require any additional information from the operator.
- Output: The application module will generate the online crude composition of each crude tank and its properties, historical trends of crude tank inventory of each tank, graphical display of crude tank farm operations, and lineup of all tanks either from a ship or to units.
- Information Flow: Figure-5 shows the flow of information for the crude tank composition and inventory monitoring module. Figure-6 and 7 show examples of operator interfaces for the information of composition and inventory of the crude tank. Figure-8 shows the online tracking of crude tank inventory for the past 30 days.
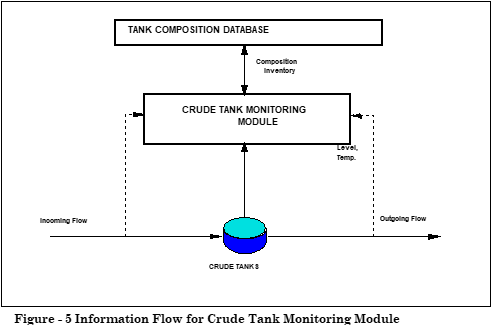
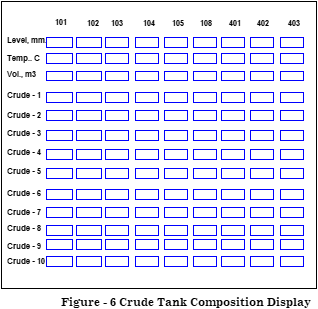
Crude feed quality control (tanks-to -crude units blending)
The purpose of this application module is to control and optimize crude feed to the crude units by blending crudes from various crude tanks. This application will control crude feeds to two crude units simultaneously based on their target density and operating conditions. The application will use the feedback from the density analyzer of the crude feed to each unit to adjust the crude blend ratio for control.
- Interface’s: The application will interface with the planning and scheduling module, tank gauging system, crude tank database, and linear programming algorithm.
- Input: The application module will require the operator entries for the target crude feed density and flow rate for each of the crude units.
- Output: The application module will generate the online composite crude composition of the crude feed to each crude unit and its estimated properties.
- Information Flow: Figure-9 shows the flow of information for the blending of crude from tanks to crude unit composition and inventory monitoring module. Figure-10 shows an example of an operator interface for the information of composition and properties of the crude feed to each crude unit.
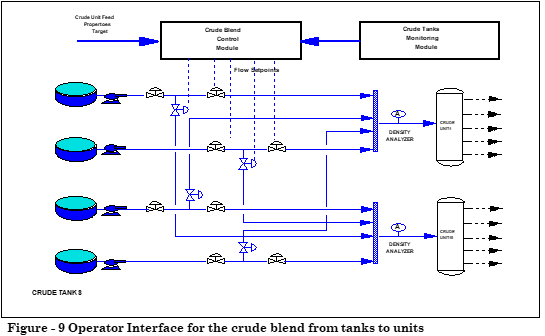
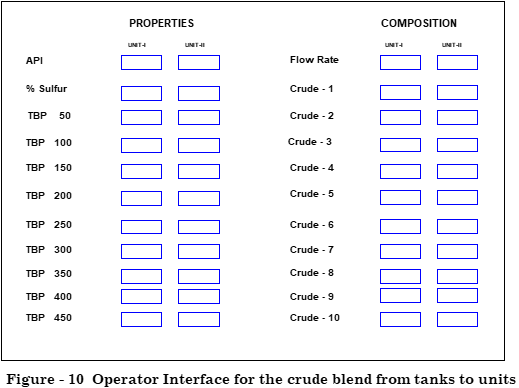
Feasibility of crude blending in a refinery
The cost/benefits analysis to determine the feasibility of crude blending is complex and different from the product (gasoline, middle distillates) blending because of operational and physical constraints. It is very important to analyze these constraints in detail to determine the feasibility of crude blending. A scoping study should examine at least 4 months’ data of oil movement & storage activities in the crude oil area.
Operational data analysis
Oil movement & storage (OM&S) activities in the crude oil area should be analyzed for the following information.
- Types of OM&S activities and their relative distributions
- Crude oil types and their receipt volumes
- Schedules of marine unloading
- Schedules of crude types and their feeding to crude units
- Relative percentages of transferring slop ( volumes and occurrence frequencies ) from other process units
A typical refinery handles 40-50% of all products by weight with only 5-8% OM&S activities in the crude oil area. Major transfer activities in the crude oil area are: “tank to tank,” “tank to unit” and “unit to tank” and constitute about 85-90% of all crude oil area activities.
Operational and physical constraints
The result of the crude oil area transfer activities will determine the basis for the feasibility of crude blending as it will show the operational and physical constraints for its feasibility. Some of these constraints are discussed below for a typical refinery.
- The insufficient number of crude tanks for blending – This may be due to types of crude processed, downstream processing demands, ships’ schedules, etc.
- Lack of free space to install new crude tanks and/or pipelines – This may be a physical limitation despite the economic feasibility of crude blending.
- Segregation of crude types and allocation of specific crude tanks for them–Low sulfur crude and high sulfur crude will be kept in separate tanks to avoid contamination.
- Recirculation and “tank to tank” transfer activities – Recirculation of the feed tank may limit its use for blending.
- Configurations of “tank to unit” activities in crude oil – This is an operational constraint as it determines the feasibility of blending crude before feeding to the unit. For a typical refinery with two crude units, there are four types of “tank to crude unit” transfer activities and are as follows:
-
-
- One tank feeds to one crude unit only.
- One tank feeds to both crude units.
- One tank feeds to both crude units simultaneously and another tank also feeds to one of the crude units.
- Both tanks feed to both units simultaneously
-
Figure-11 shows the configurations of “tank to unit” transfer activities.
Configurations of blending schemes
It is clear from the previous section that the configuration of the blending scheme for crude depends greatly on the operational and physical constraints and may defeat the economic advantages. There are three following scenarios for the blending of crude.
- “Ships to tanks” blending
- ‘Tank to tank” blending for crude feed
- Inline blending from tanks to units
Figure-12 shows various schemes for unloading and blending crude from ships to tanks. Transfer types I and III unload crudes into tanks directly and later may be blended from tank to tank to prepare the final crude feed. However, integration of scheduling and tank inventory, and composition modules, as discussed earlier in this blog, will be necessary to implement any blending schemes. Such integration of application modules would alleviate some of the physical and operational constraints.
At any given time both physical and operational constraints govern the feasibility of one blending scheme over another. For example, physical constraints such as the availability of crude tanks will determine the feasibility of crude unloading and its blending into tanks at the same time or later for tank-to-tank blending configuration. On the other hand, operational constraints will determine the need for inline blending to crude units.
It is important to realize that although the integration of all modules discussed earlier in this paper would stabilize the quality of feed to distillation unit to achieve the product quality targets and improve the operational stability of the distillation unit, there may be a situation where an individual module is implemented for one reason or other. For example, if physical constraints do not permit for “ship to tank” or “tank to tank” blending of crude oil, inline crude blending to a crude unit can accomplish the same objective to a certain extent.
It is worth noting here that tank-to-tank bending has more degrees of freedom (depending upon the number of available crude storage tanks) than inline blending to crude units. In inline blending, crudes are blended usually for density control purposes only since the API density determines the crude distillation curve.
Conclusion
Crude blending is different and complex in implementation than product blending and an extensive scoping study should be conducted to determine its technical feasibility, cost, and benefits under the existing physical and operational constraints in a refinery. Adequate data analysis of current crude oil transfer operations is necessary for a thorough understanding of the scope of the problem. Undoubtedly, greater economic benefits can be realized if the scope of crude blending is looked at from an overall integration of operations from the scheduling of crude ships to final product shipments.
#CrudeBlendingControl #CrudeQualityControlIntegration #CrudeDistillationUnit #ProductBlendingOptimization #CrudeFeedQualityControl #RefineryCrudePlanning #CrudeTanksQualityControl #OperationalDataAnalysis #TankBlendingConfiguration #ApiDensityControl
1 2 3 4 5 100%
1 2 3 4 5 0%
1 2 3 4 5 0%
1 2 3 4 5 0%
1 2 3 4 5 0%