Introduction
Refineries worldwide are compelled nowadays to re-examine their gasoline blending control system to meet the increasingly stringent local or export regulations and also to improve the plant’s bottom line by minimizing gasoline quality giveaways. Since the ROI of either upgrading a manual system to an inline blending system or from an inline blending to an advanced blending control system justifies the upgrade project, it may not produce expected results if the enterprise is not “ready” for the change. It is not very uncommon that after substantial investment in the project, the upgrades in the blending control system may become dormant, and blend operators switch to some hybrid blending methods due to a lack of sustained commitment and support within the enterprise.
This blog is a discussion of a gasoline blending control system and how the technologies of change management and systems in partnership can deliver improved results for the business. Part I discusses the methodology to assess the organization’s capability to implement or upgrade to an advanced gasoline blending control system from existing installation and plan strategies to sustain the benefits for years to come. This blog is based on a management and technical study conducted by the authors of this blog for an actual mid-size refinery in North America. The refinery has basic regulatory inline blending system in operations for many years and wanted to know what it will take to upgrade their system to a world-class advanced gasoline blending control system. Is it hardware and software alone or organizational system changes as well?
This blog will also discuss the required “enterprise change” and Part-II will discuss the hardware/software requirements as both are absolutely necessary for a successful upgrade implementation and sustainable Return on Investment (ROI).
Objective
The capability assessment process was originally developed in conjunction with strategic planners who observed that businesses frequently failed to execute the plan effectively, despite a systematic approach to planning strategies. It was their opinion that when the strategy called for a new direction, the organization frequently failed to build the required capabilities to carry out the plan. Capability assessment and capability development planning were developed in order to improve strategic performance. Since our initial work utilizing this process, we have successfully applied it to major projects for clients with good success.
The refinery had contacted organizations of both authors and was interested in using the capability assessment process to plan for upgrading the blending capabilities of the refinery. The management felt there was an opportunity to capture the value and improve product quality. Their previous experience with the process led them to believe that it would be helpful in planning for improved blending performance. What was unique about this study was that the study combined numerous capability assessments experience of Navigator Management Consulting, Inc. in the petrochemical industry and domain expertise and experience of Offsite Management Systems LLC who also has developed and commissioned sophisticated automation software systems for the refinery blending control and optimization. Prior to the beginning of the project, the refinery management sponsors for the project identified strategic criteria for improved blending performance.
Team composition
A team of refinery employees met six times in four months duration. The team consisted of the following members Technical Services Manager who served as Team Leader, Fuels Optimization Manager, Pump Room technician, Blending Supervisor, Lab supervisor, IT supervisor, Organization capability consultant, and the Blending Technical Consultant.
Team members represented all of the significant functions which would need to be involved in order to ensure that a comprehensive assessment was done. Team members were also told that a part of their role was to act as a representative for their respective function and to communicate during the course of the project with other members of their groups in order to get complete information and build commitment to the plan. Team meetings were conducted on alternating weeks in order to allow time to consider the previous weeks’ output, gather information required to complete assignments, communicate with others, and get feedback.
Key results area
Prior to beginning the blending capability study, the technical consultant had done a preliminary assessment of the level of automation in place at the refinery and confirmed that indeed there was a significant profit opportunity. The refinery management through discussion with the Organization Capability Consultant had said that the key results to be accomplished through the process and the subsequent project would be to Optimize Financial Performance of Blending Operations by:
- Ensuring adequate and aligned resources
- Consistently meeting market demand
- Minimization of a giveaway by maximizing octane bonus and optimizing blend economics
- Optimize octane supply
- Minimize re-blending by minimizing cycle time and optimal blending to specifications
These expectations served as the basis for the organization’s capability assessment. The entire process was divided into two distinct phases, namely, Assessment and Development to achieve the above expectations in a systematic approach.


Figure 1. Organization Capability Assessment Process
Phase 1 – Assessment
Step 1 – Identifying capabilities required
Figure -1 shows the capability assessment process. At the first team meeting, an overview of the process was presented to educate the team about the process and to review the goals set out by the refinery management. The first step was to identify the capabilities required for the effective execution of those goals. This was done through brainstorming and discussion by the team members. The team identified a number of required capabilities. The capabilities identified fell into the following six categories:
- Building and maintaining blend and optimization planning tools
- In-time availability of tank qualities
- Accuracy of analyzer and field instrumentation
- Adequate equipment capacity
- Optimum manpower usage
- Organization metrics for effective communication
Step 2- Defining capabilities
Once the capabilities had been identified the team was asked to provide some specifics to define these categories. This step ensures that the team is in agreement about what is included in each of the capabilities as we move further along the assessment process. This step frequently helps the team clarify what functions are covered by each capability. It is not unusual for the capabilities to be revised at this point in the process which can include consolidation, modification, or addition to the capabilities.
Step 3 – Relating capabilities to the key results
After the capabilities were identified and defined, the team was asked to identify which capabilities support the management key result areas. This step provides a check for the completeness of capability identification and can also show preliminary importance based on the number of key result areas supported by the various capabilities. The result of this step is a matrix showing the relationship between key result areas and capabilities. At the conclusion of this step, the team leader was asked to review the results of the teamwork with the management sponsors to get their feedback and concurrence with the capabilities. In this case, the discussion among the team leader and management resulted in additions and modifications to several capabilities.
Step 4 – Capability assessments
The team was ready to evaluate the capabilities after completing the definitions and the key result/capability matrix. The evaluation looks at two dimensions for each of the capabilities, importance, and performance, i.e., how important to the key results area is each of the capabilities and what the current level of performance is. A question that frequently arises for performance is its comparison to what? The options usually are best in class or relative to what we need to be successful. The problem with best in class is that the data on competitor’s capabilities is frequently not available so the usual way of approaching this is to say it is relative to what you will need to be successful. Each team member was asked to do this assessment for each of the capabilities they have identified. When they have completed their individual assessment the data is summarized in a spreadsheet and entered into a plot shown in Figure-2. Individual assessment is done to ensure that team members have an opportunity to form and express their own ideas about the capabilities.
This plot in Figure-2 shows 13 items ranked on performance and importance. The dissecting diagonal lines create three quadrants Surplus, On Track, and Gap. This data is shared with the team as a way to start the discussion. Of particular importance are items where team members’ rating varies widely. Where there are large differences they are discussed and ranking can change as a result. In this plot, the items were arranged numerically to have the number one items as the capability with the biggest gap.
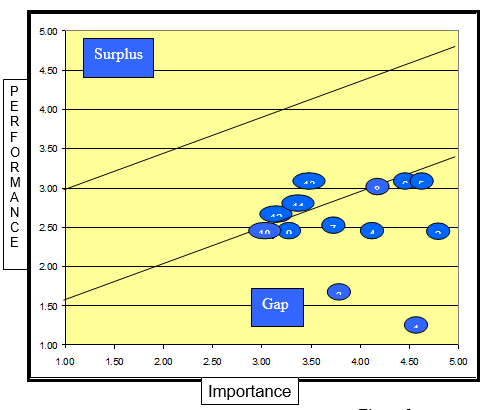
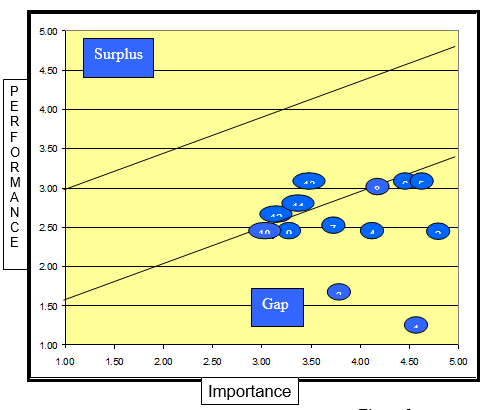
Figure 2. Blending Capabilities Assessment
The capability assessment stage was an example of a part of the process that benefited significantly from having the technical consultant (Offsite Management Systems LLC) as part of the team. He was able to contribute information about how this refinery compared to the industry in relation to the state of blending automation the refinery had at the time of the study.
Step 5 – Prioritizing
Once the assessment discussion was completed, the team made a decision about which capability gaps need to be addressed in the near term and which capabilities are sufficient for the successful execution of the key result areas. Of the 13 capabilities identified, eight were identified as needed to be addressed in the near term in order to improve blending performance. Five were deemed to be adequate at that time. There was a good bit of discussion among the team about the interdependencies between the various capabilities, i.e., a high-quality planning tool without reliable analyzers, instrumentation, and equipment capacity would not produce the results desired.
Step 6 – Defining current and future state
The final step in the assessment phase of the process is the definition of current and future states. The assessment graph and subsequent discussion provide a basic assessment but we have found it useful to describe the current level of functioning and the desired future state provides useful descriptions of the gaps that exist. It is particularly helpful in helping the team discuss gaps with the management team who will eventually approve expenditures for capability projects. This step is also followed by a management review to ensure alignment.
Phase 2 – Development
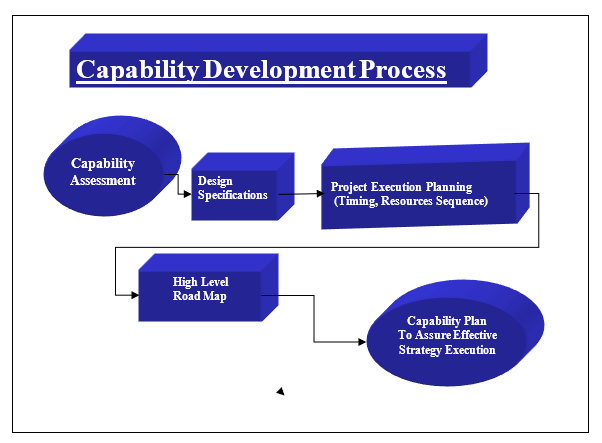
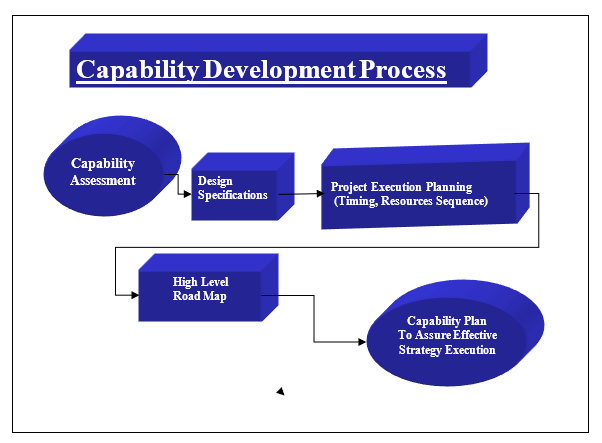
Figure 3. Capability Development Process
Figure 3 shows the steps of the capability development process. The input as shown is the assessment the output is a plan for what when and how the capabilities will be developed by the organization as well as a high-level roadmap for sequence and timing. On one important note, it is important to enquire what other initiatives the organization has currently or is anticipated in the near future. These must be factored into the plan in order to give a realistic estimate of when deliverable s can be expected. It also can serve to provide integration with other initiatives.
Step 1 – Design specifications
The first step in planning for capability development is to build a set of capability design specifications. Like engineering specifications, it is to identify the requirements for the project. It has been our experience that when organizations attempt to improve performance and build capabilities they limit their thinking to those changes they are familiar with, i.e., technology, organization structure, or training. Our approach is to take a total systems approach in thinking about design requirements in order to get alignment across all components. This approach improves the probability of success significantly.
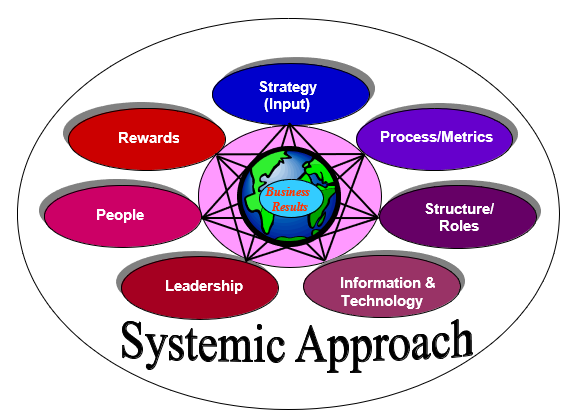
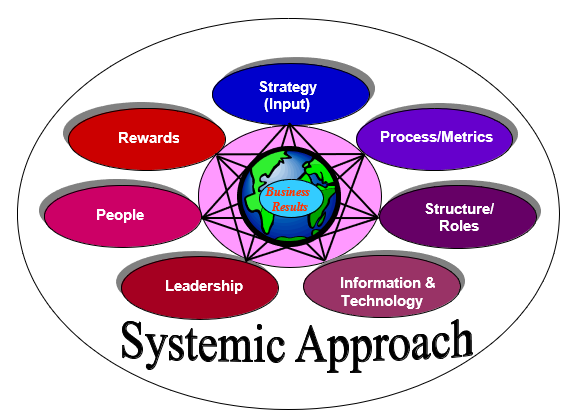
Figure 4. Systematic Approach
Figure-4 shows the components we looked at to determine design requirements. Strategy or Key Results areas are shown as input to the process. While requirements are not necessarily identified for each category, the model serves as a check for completeness. We also have a category for other assets which is not shown here. The team was asked to brainstorm design requirements for each of the capabilities identified as needing attention. In the case of this refinery, we had eight capabilities needing near-term attention. This work was begun in a team meeting and team members were then asked to work in sub-groups offline and in conjunction with colleagues to develop the design requirements. Design requirements were reviewed by the entire team in the next meeting and feedback was provided by each of the subgroups.
Step 2 – Project execution planning
Once the design specifications were complete owners for detailed plans were assigned and asked to develop detailed plans for building the capabilities in the manner shown below as an example:
Capability: #MinimizationQualityGiveAway #ManpowerRefineryManagement #BuildingMaintainingPlanningTools #RefineryManagementAnalyzer #RefineryFieldEquipment #RefineryAutomationBlending #OffsiteManagementSystems #CapabilityDevelopmentPlanning #RefineryBlendingOperations #OptimizeRe-Blending
1 2 3 4 5 100%
1 2 3 4 5 0%
1 2 3 4 5 0%
1 2 3 4 5 0%
1 2 3 4 5 0%