Introduction
One barrel of crude oil produces 80-85% of blended fuel products such as gasoline, diesel, and fuel oil. Gasoline fuel production is between 45-55% of one crude oil barrel. These fuel products are made by blending 6-12 components that are produced in the refinery process units and have different qualities such as RON/MON, RVP, distillation points, olefins, aromatic, etc., to meet the final product specs. Each of these quality specs is controlled by regulatory agencies such as EPA and is based on environmental factors and proper functioning of vehicles in all weather conditions. For example, different car models require different octane ratings of the gasoline fuel from 87 to 95 Octane to operate without knocking and are independent of the region or the season. On the other hand, RVP or Reid vapor pressure has different specifications based on region and season alone and is independent of the vehicle models.
Gasoline properties and significance
Reid Vapor Pressure (RVP) is a measure of the volatility of the fuel and has an absolute maximum value of atmospheric pressure of 14.7 psi (101.35 kPa). It has both minimum and maximum specifications and varies from Winter to Summer. In the cold temperature of the winter season, it is important that fuel has enough vapor phase to start the engine while in summer too much vapor phase will create vapor lock. Naturally, RVP specs are higher for the winter season than the summer season and can vary from region to region. Refiners sometimes must make 20+ boutique grades of gasoline with different RVP specs alone to meet the regional and seasonal demands of gasoline. Table-1 shows an example of gasoline qualities, range, and types of specs and their environmental and vehicle-related significance.
As we can see from Table-1 that RVP is the only direct gasoline specification that has regional and seasonal maximum values as controlled by EPA. The maximum value of RVP for most states is 9 psi but also has lower values of 7 and 7.8 for few regions. The RVP limit is extended to 10 psi if the formulation has 9-10% ethanol. The addition of ethanol in the gasoline reduces the vapor pressure of the ethanol-gasoline blend and lowers the temperature of critical V/L of 20 to avoid vapor lock.


Table 1. Gasoline Properties and their Significance
Regional and seasonal RVP specs
The controlled period for the summer blend RVP is as follows:
- For refiners and terminals – May 1 to September 15
- For retailers and wholesalers – June 1 to September 15
However, the RVP controlled period in California is from May 1 to October 31 with the different periods for different air basins and counties within that timeline to start earlier like April 1 or late like June 1, and end late like September 30 or October 31. Figure-1 show variation of RVP spec for various California air basin and counties. EPA limits the highest RVP summer value as 9 for all states other than California and we will use this historical data for California to discuss the concept of this blog.
Figure-1 shows that refiners start ramping down the gasoline production with lower RVP gradually to meet May 1 deadline for the summer spec and again start ramping up from September 15 or later, as the case may be, for winter gasoline blends. During the summer period of May 1 to September 15, refiners produce gasoline blends with a constant RVP value of 9 psi in most states.
RVP can be increased for winter blends by adding externally or in-line blending as butane can blend with gasoline in liquid form, but refiners face the challenge of lowering the RVP of winter blend ramping down to summer blend as butane cannot be simply taken down. Hence, refiners use lower RVP value components in the winter blend to meet summer specs during the ramp-down period. These lower RVP value gasoline are expensive and hence the price of gasoline is higher in summer than is in winter. Figure-2 shows the variation of mid-grade (RON 87) over the year 2018. The gasoline prices synchronize with the transition of winter grade to summer grade.


Figure 1. Regional and Seasonal RVP specs


Figure 2. Variation of 2018 mid-grade conventional gasoline
Tangible benefits
The refiners realize the tangible benefits of butane blending only during the blend RVP ramping stage for the period of September 15-December 31. The tangible benefits come from the fact that they can add butane to the gasoline pool than the LPG pool as there is an average price spread between gasoline and LPG of about $2/gal as based on the average winter price of gasoline and butane to be $3/gal and $0.94/gal, respectively.
We used a simple 2 by 2 algebraic equation to blend mid-grade (RON87) with butane for octane and RVP values. We used a linear blend model for RVP for simplicity and illustrating the order of magnitude of tangible benefits at various levels of winter blend RVP. The actual butane blending control system uses a non-linear equation for the control of the final blend RVP.
Figure-4 shows the results of such calculations and shows that tangible benefits can vary from 100K$ to 6M$ for a gasoline batch of 100KB and the % butane in the gasoline blend can be as high as 11-12% based on blend RVP value. The tangible benefits increase during the winter period RVP ramping steps. We also estimated the refiners can realize a maximum tangible benefit of 600M$+ for 100+ batches of 100KB/day gasoline for the entire duration of the winter season. These huge benefits simply should not be ignored by the refiners and retailers as it is paid off in no time for a butane blending system. We will also discuss a representative butane blending system by TechnicGlobal in this article.


Figure 3. Butane Blending Tangible Benefits
Process of butane blending
The process of blending butane in gasoline depends on the source of butane in a refinery. Large refineries manufacture and store Butane onsite. Butane comes from many different process units like the Distillation unit, FCC, Coker, and Reformer, in the refinery, as well as from outside sources such as natural gas. However, small refineries, wholesalers, traders, terminal operators do not manufacture Butane and resort to buying Butane from external sources. Regardless of the supply chain to procure Butane, it is blending into Gasoline in one of the following manners, Each of these blending modes has pros and cons and must be weighed against the economics, flexibility, safety, and risks.
Inline tank-to-tank Blending – This is a common mode of blending Butane as one of the components along with others. This mode has the advantage of an optimal recipe, operational convenience, better control, and overall management. On the downside, it requires well-tuned and refinery-specific customization of blend models. This mode can also be used if the refinery buys Butane from external sources and loads it into its Butane storage tanks or blends directly from temporary storage such as tanker trucks or railcars. This model also has the danger of violating specs for Summer grades for ill-configured blend models.
Blending at the terminals and pipeline – Both refineries and wholesalers practice this mode alike. Traders use this mode to blend butane directly into purchase gasoline to gain economic benefits for the winter-grade gasoline. This mode requires precise measurement of RVP and monitor of final RVP values to realize maximize giveaway benefits. This mode of Butane Blending is discussed more in detail in the next section.
Blending infrastructure
The terminal butane blending must consider the following aspects of its infrastructure.
Storage – For cases where the refinery does not manufacture and store Butane onsite, the use of temporary storage in the form of trucks or rail is the next choice. The main benefits of using rail, if the facility exists, are the storage capacity coupled with the ability for the tanker car to remain at the site for extended periods. The other temporary method is the use of tanker trucks. This method certainly has the lowest cost. But it has the disadvantage that the supplier may not supply the tanker for an extended period and may have only limited tanker capacity.
Transfer – The transfer of Butane from truck or railcars faces the following problems and the terminal operator must be considered the design of the facility and the blending operations.
The existing transfer system may not be best for the blending system. The exiting pumping system may have designed for high flow loading and unloading and hence would be unsuitable for the turn-down requirements of a metering blending system.
The butane transfer should be controlled at a pressure higher than the gasoline pipeline as Butane will bond with gasoline only in the liquid phase only. The use of a vertical turbine pump is recommended to eliminate many problems due to its inability to create vacuum conditions. Care should be taken for overflow prevention, strainers, and shut-off valves prior to the pump.
Transfer from a rail car is possible only from the top of the car. Suction with a vane pump is certain to cause the creation of a gaseous phase with the required lift. A small buffer tank and the correct pumping method ensure the delivery of only liquid Butane to blend.
Figure-4 shows a typical blender system with a 12” pipeline for the gasoline stream and a Coriolis flow meter.


Figure 4. Blending System Hardware
Metering, blending, and analysis
The Butane vapor phase must be returned to the storage tank using a Coriolis flowmeter and vapor recovery system. It is important for safety and environmental risk considerations.
The Coriolis flowmeter handles two-phase flow and provides precise estimates of its proportion to liquid.
As we had discussed earlier, butane % in the blend can vary from 2-11% based on the gasoline RVP and final RVP specifications. The control system should be able to manage low and high values of Butane additions in the blend.
Final homogenous mixing of the blend is achieved by higher pressure of the Butane injection stream and ensuring the gasoline stream does not have backpressure greater than Butane pressure at the operating temperature by using an orifice plate of throttling valve for the gasoline stream.
The system uses two online RVP analyzers, with a repeatability ≤ 0.50 kPa (0.073 psi), as stand-by, comparative analysis of RVP and faster cycle time by using the lead-lag methodology. ASTM standards D6378 and ASTM detail the measurement methods for Gasoline and Butane RVP.
Figure-5 shows a typical control and analysis system with fast loop pumps for Butane, Gasoline, and the Blend.


Figure 5. RVP Online Analyzers System
Control system
The control system should be designed as mission-critical not only due to the regulatory and safety implications caused by a butane-rich blend but also due to the fact that revenues occur in batches during the year. A typical butane blending operation proceeds as follows:
The controller is placed in ready mode and it immediately samples the butane feed, measuring and recording its RVP.
After the butane is measured, the system sits idle waiting for gasoline flow. Once detected the raw gasoline is sampled and its vapor pressure and density are recorded. The system begins to add butane to the flow. The amount of butane delivered is calculated through a specific algorithm equating the density and RVP of the feed streams along with certain assumptions on their composition.
At this point, the system begins analyzing the homogenized fuel and adjusts the transfer of butane to match the overall target given the value of the blend already transferred to the storage tank.
The system re-enters idle mode when the gasoline flow is stopped. A batch report is generated and stored on the computer. The deviation between calculated and actual RVP is used by the computer to modify its stored algorithm in preparation for the next transfer. For systems that directly feed tankers. The next instance of gasoline RVP is assumed to be the same and thus steps 1-3 are bypassed.
Figure-6 shows a typical graphical user interface display to control and monitor the butane blending system.
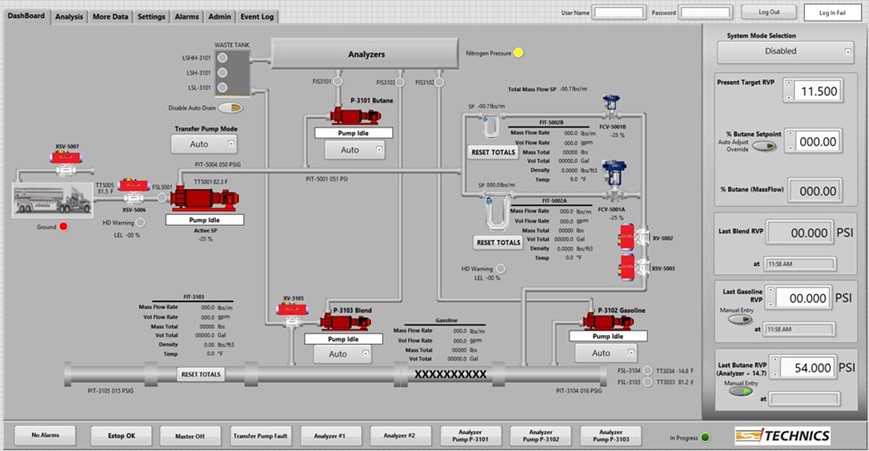
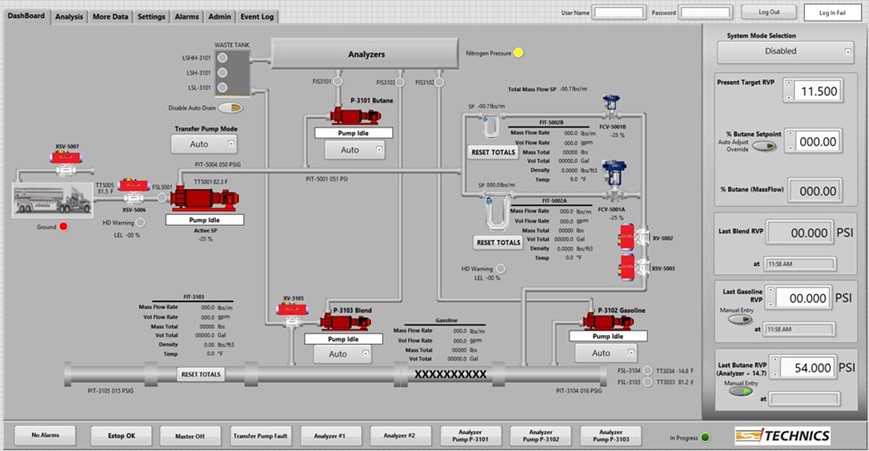
Figure 6. Graphical User Interface for Blending System
Conclusion
This article has discussed the concept of Butane blending with respect to its significance for the gasoline properties, tangible RVP giveaway benefits due to season, and regional changes in RVP specs from Summer to Winter gasoline grade. We have also discussed attributes of a typical Butane blending infrastructure with respect to butane storage options, hardware, quality measurement, and control system. We have shown that tangible benefits from butane blending can be as high as 500 – 600 M $ during the entire winter-grade season and payoff from the installation of a butane blending system can be as low as few weeks.
References
- “Reid Vapor Pressure (RVP) Control Periods for California Air Basins and Counties”, http://www.arb.ca.gov/desig/adm/basincnty.htm
- “Gasoline Reid Vapor Pressure”, https://www.epa.gov/gasoline-standards/gasoline-reid-vapor-pressure
- Product literature as provided by Global technics (www.technicsglobal.com)
Authors
Tom Edwards, President Technics, Inc.
Dr. Suresh S Agrawal, CEO, Offsite Management Systems LLC
Additional Resources
- Butane Blending – Enroll in audio-video eLearning of the topic – Click Here
- Download Butane Blending Blending Calculator – Click Here
#GasolineOctane #ButaneBlending #Ethanol-GasolineBlend #In-LineBlending #CoriolisFlowmeterMeasurement #ButaneInjectionStream #VaporRecoverySystem #RvpOnlineAnalyzersSystem #TerminalsBlendingOperations #SeasonalRvpSpecs #RegionalRvpSpecs
1 2 3 4 5 100%
1 2 3 4 5 0%
1 2 3 4 5 0%
1 2 3 4 5 0%
1 2 3 4 5 0%