Introduction
The automation of tank farms for refinery oil movement and storage in off-sites consists of several technologies (Rys, 2018)2. These span factors like systems of transactional business information, supply chain systems, temperature, safety systems, advanced control/optimization level and flow measurements, Distributed control systems (DCS), Programmable logic controller (PLC), pre-set controllers, etc.
Refinery off-sites are usually said to play a key role in production monetization. Hence best preparations are needed to facilitate these technologies to work together to help the flexibility of overall operations (Rys, 2018)1.
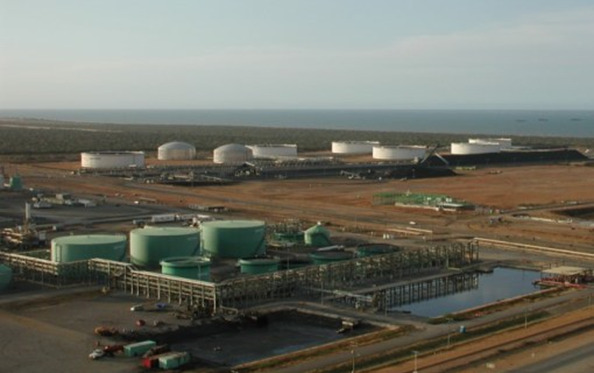
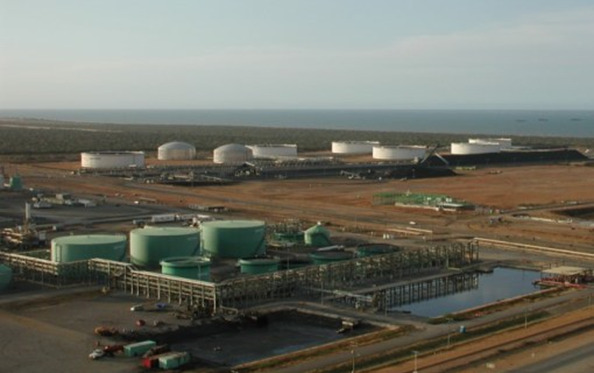
Figure 1. Refinery Offsites Tank Farm (Rys, 2018)2
Refinery oil movement management system
The system that manages all LPG storage, all pipelines, and crude oil storage tanks, spheres in the tank arm area. It also manages the movement of all intermediate/finished products. It is known as Oil Movement Systems of Offsite Area Management Applications. OMS gives a collective environment for the offsite tasks and also provides an overview of all the activities, instructions, tasks, data, and imperative events within the premises (Iogsolutions, 2019).
The tank farms in any refinery/petrochemical plants are used to store the inventory which is worth billions of dollars for liquids such as crude oil, intermediates/finished products. On a routine basis, the inventory of the above liquid assets is tracked in real-time and carried within/beyond the site boundaries. It is a crucial factor to manage these assets not only from safety (equipment, explosion, spillage, burn-outs) point-of-view but also for reconciliation of receipts/dispatches to avoid errors and thereby maintaining a profit margin.
OMS proves to be of great use for users to decrease the inventory requirements with improved planning and timing, enhance the offsite area by auditing in real-time, enhance the people safety, processes, and equipment with combined safety/security solutions. It also takes care of environmental risk through identification/protection/mitigation systems (Iogsolutions, 2019).
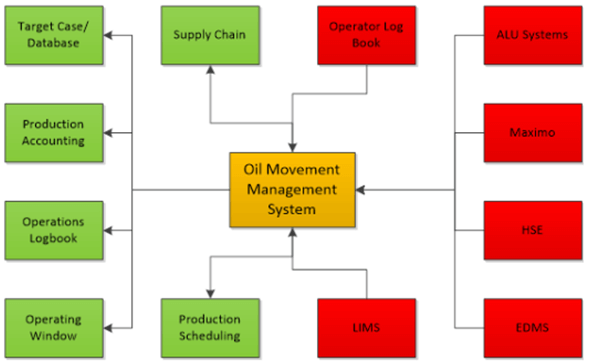
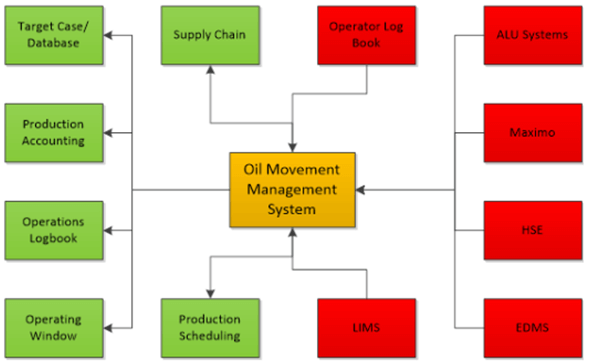
Figure 2. Oil Movement Management System (Iogsolutions, 2019)
The complexity of refinery oil movements
It is obvious, that the tank farms must be intact and environmentally compliant. Without delaying or taking product contamination risk, it is very essential to plan beneficial oil movement and also piping line up and implement the plan. The piping system topology is specifically known and read by the tank farm automation system due to regular operations. The condition of all pumps, control valves, block valves, and piping systems should be monitored. Supply chain planning should not only check for any defective pumps/leaking valves, but it should also check for other simultaneous movements of material that could interrupt the line-up of other movements (Rys, 2018)1.
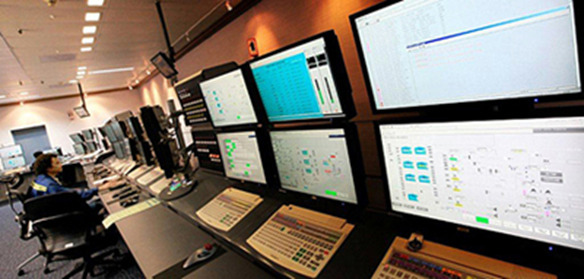
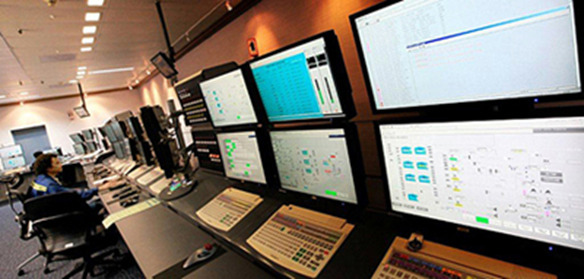
Figure 3. Central control room (CCR) for Oil Movement System (YoKogawa, 2019)
The piping flow paths operation includes booking/reserving piping segments, valves, and pumps for the span of refinery oil movement. Organizing a number of product movements can generate many beneficial solutions with various movement paths at a time. The specified pipe segments, valves, flow meters, and pumps are selected. They will have limitations on the flow rates concerning appropriate paths.
This can be a crucial decision that affects the span of a refinery oil movement. For example, a blending operation consists of lining up many rundown tanks to a blend header. It goes down into a product storage tank. Identifying a small pump/small flowmeter for the alkylate blending component may lead to the blending rate limitation. It may even extend the needed time for product tank filling. This may affect future oil movements by tying up the required equipment. In the context of oil movement and storage, this is one of the various situations that may arise. A number of technological options are available for these difficult situations (Rys, 2018)1. These include the following:
Tank gauging systems
The basis for effective automation is being aware of the real-time inventory in a tank farm. For measurements of level, there are a number of technologies. Out of which, various technologies consist of “strapping tables.” For converting the tank level to the stored volume, the table is used. The tanks are filled, there is expansion/distortion. To maintain accurate volumetric measurements, temperature compensation is required (Rys, 2018)1.
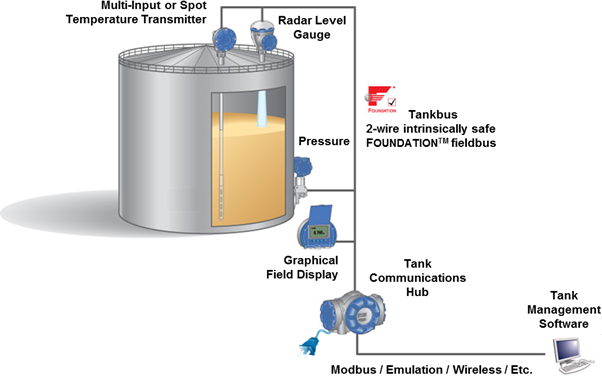
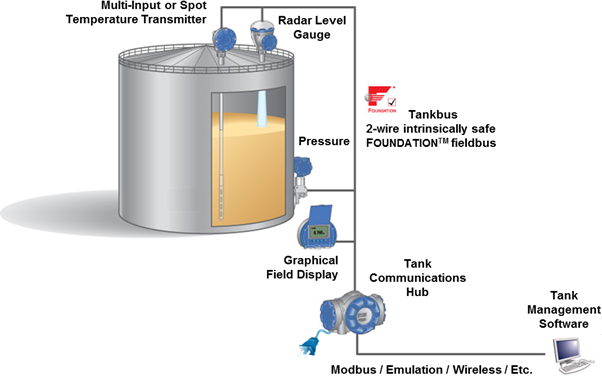
Figure 4. Oil Movement and Tank gauging (Segal Petro Niru, no date)
Tank gauging solutions are as follows:
- Level switches (D/P, capacitance, float…)
- Dip tube with gas flow back pressure
- Nuclear
- Capacitance
- Float Inductive
- Buoyancy float (servo or tape)
- Ultrasonic
- Hydrostatic, D/P head-based level
- Radar/microwave
A guide is available. It may help operator/clients/customers in the context of selection of the most useful tank gauging systems as per the requirement.
Tank information systems
The product quality information and the tank level/volume information are brought together by Tank information systems (TIS). Using analyzers, it may be computed/measured. Using lab analysis, it may be estimated by periodic sampling. There is a GUI (graphical user interface). Various automation functions are connected using GUI. To support other tank farm applications, the TIS provides a useful database, that is real-time (Rys, 2018)1.
Oil movement monitoring and yield tracking applications
All the active movements with alarms concerning various issues can be shown with Movement Monitoring/material balance as well as Yield Tracking Applications. This also helps in having records concerning the history of all movements. Mass balance checks are used for ensuring the decrease in volume in the source tanks, matches with, and the volume gained at the destination tank and flow metering.
To follow the standard conditions, the flowrate meter can be adjusted using the accepted practices. In the context of customer’s orders, the movement can be located (Rys, 2018)1.
Path management/movement automation
Path management generally applies procedural automation. It is used to stop the refinery oil movement when it is completed, start the flow and facilitate movement line ups. The application does booking particular equipment.
The total tank farm piping networks need to be understood to the full extent. Path management cannot be automated without instrumented hoses, valves, pumps, and other assets. Hence, confirmation is required so that the manual procedures can be completed. For example, to initiate an oil movement, some hose connections are needed. But the operator needs to confirm first whether appropriate hose connections are there or not (Rys, 2018)1.
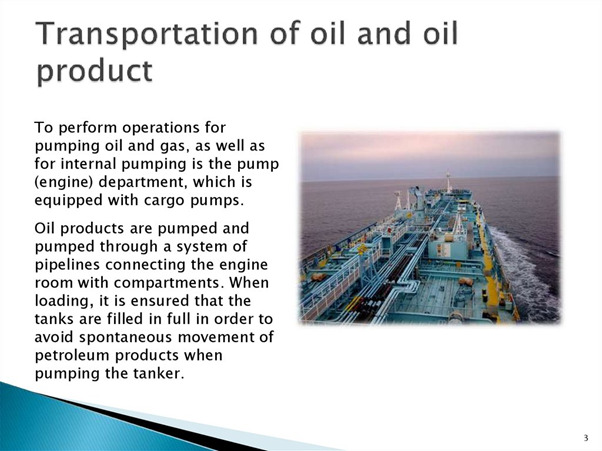
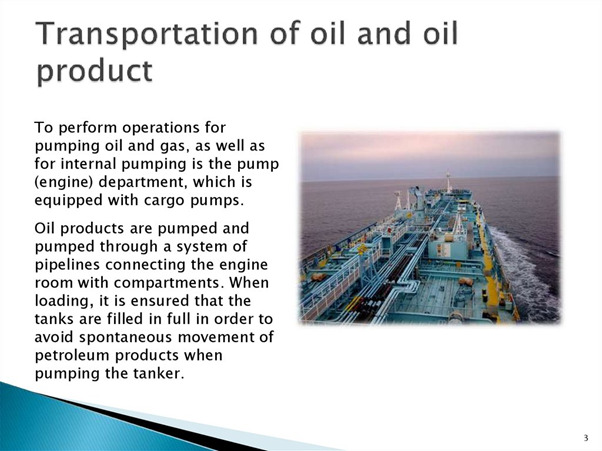
Figure 5. Transportation of oil and oil product (Third group, no date)
Controlling blend ratio
Refinery tank farms normally have distillate blending systems/gasoline. A ratio control scheme is applied by a refinery. It is a simple scheme.
In this case, components are selected. Then they are mixed into a blender header. It is done prior to being sent to a product storage tank/ pipeline. On the basis of flow measurements, the blend components have a volumetric ratio during the movements of this blend. In a simple way, the flow moves up to a blended rate. Then the same blend rate is continued. This happens till the blend reaches the end. Then it flows back down to a trickle. This happens before the blend stops.
A number of schemes can handle a condition where one or more components will not keep up the desired flow, which would avoid the desired blend ratio for being accomplished. For example, to slow down the blend rate to have the desired blend ratio, “pacing” control may be utilized (Rys, 2018)1.
Optimization of blend
A normal blend ratio control does not react to changes in the quality of the product or errors in measuring the qualities of the component tank that is used to estimate the blending ratios. Different executions use online analyzers at the blend header. This is done to control feedback. This assures that the blended product meets all the requirements of product quality.
Many configurations estimate the values of some/all blend properties in the product tank as it fills. This is done on the basis of the analyzers. Blend header is having connectivity to these analyzers. Optimization of the blend may be achieved for the lowest cost of components. There may be another objective like the lowest variation from starting ratio (Rys, 2018)1.


Figure 6. AMB and Oil Management system (YoKogawa, 2019).
References
- Iogsolutions. (2019). Oil Movement Management System, https://www.iogsolutions.com/manufacturing-execution-systems/oil-movement-management-system, Accessed on Nov. 26, 2019.
- Rys, R. (2018)1. The Oil & Gas Supply Chain: Oil Tank Storage and Movement Best Practices, https://logisticsviewpoints.com/2018/03/29/oil-tank-storage-and-movement-best-practices/, Accessed on Nov. 26, 2019.
- Rys, R. (2018)2. Oil Movement and Storage Best Practices, https://www.arcweb.com/blog/oil-movement-storage-best-practices, Accessed on Nov. 26, 2019.
- Segal Petro Niru. (no date). Tank Gauging & Oil Movement, http://segalpetroniru.com/en/solutions/metering-storage-fuel-systems/tank-gauging-oil-movement, Accessed on Nov. 28, 2019.
- Third group. (no date). Transportation of oil and oil product. https://en.ppt-online.org/490430, Accessed on Nov. 28, 2019.
- YoKogawa. (2019). Achieving an Intelligent Oil Movement System, https://www.yokogawa.com/us/library/resources/references/achieving-an-intelligent-oil-movement-system/, Accessed on Nov. 28, 2019.
#Off-SitesRefinery #Off-SitesRefinery #SupplyChainSystems #RefineryDcs #AlkylateBlending #RefineryPlc #TankGaugingSystems #YieldTrackingApplications #ControllingBlendRatio #GasolineBlendingSystems #RefineryTankFarms #TisAnalyzer #GuiAnalyzer
1 2 3 4 5 100%
1 2 3 4 5 0%
1 2 3 4 5 0%
1 2 3 4 5 0%
1 2 3 4 5 0%