Introduction
A crude oil refinery receives products from tankers, pipelines, tanks, and train cars at the terminal. They could be crude oil or intermediate products needed to manufacture the end products in the refinery. These products are moved from the terminals to the refinery by an oil movements system and then crude blending, in-plant material movements, and product blending. All above operations performed in the refinery are a part of refinery offsite operations.
On the other hand, on-site operations involve the process units such as crude, FCC, isomerization, reformat, etc. Once the products are made, mostly the final fuels products, they are sent to the customer at the terminal via tankers, pipelines, trucks, and rail wagons.
Activities of refinery offsite operations
Activities of refinery offsite operations include:
- Terminal operations, which can be the shipyards, truck terminal, or pipeline
- In-plant material movement
- Tank farm management
- Fuel Products blending
- Crude Blending
- Preparation of feed and products to receive feeds and to dispatch the end products
Strategic management of refinery offsite operations
Refinery offsite operations include:
- Optimization of blending-combination
- Decreasing cost of blending
- Improvement of Product qualities. This may lead to exporting a high-quality of products (ABB, 2013).
- Timely blending will result in decreasing costs of demurrage.
- It is possible to look for opportunities concerning product sales on short notice.
- It is possible to reschedule operations.
- Blending may be done on ship/jetty. This decreases inventory costs.
- Oil movement may be scheduled easily.
- Quantities may be monitored/reported.
- Automation sequences may function better. This will lead to the operator’s better performance.
- Product contamination is not there.
- Better accounting of oil loss
- For material balances, high-quality data is used.
- It is real-time data.
Figure 2. Crude Oil Refining (Crude Oil Refining, no date)
Challenges for strategic management of refinery offsite operations
Every day there are many operations and sub-operations on a particular refinery offsite facility, i.e., circulation, heating, and line clearance. Every operation/sub-operation needs to be recorded/tracked. This will help to get timely payments from customers. Demurrage or contamination should be taken care of. This may happen due to operational errors or equipment failures.
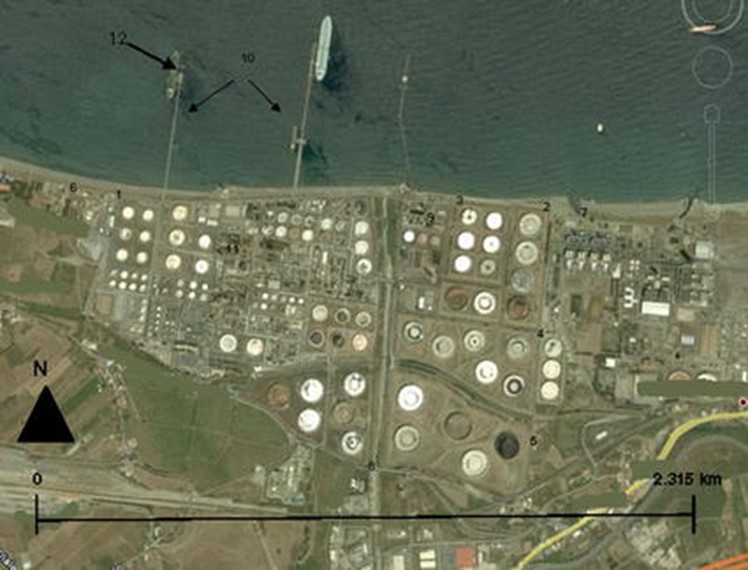
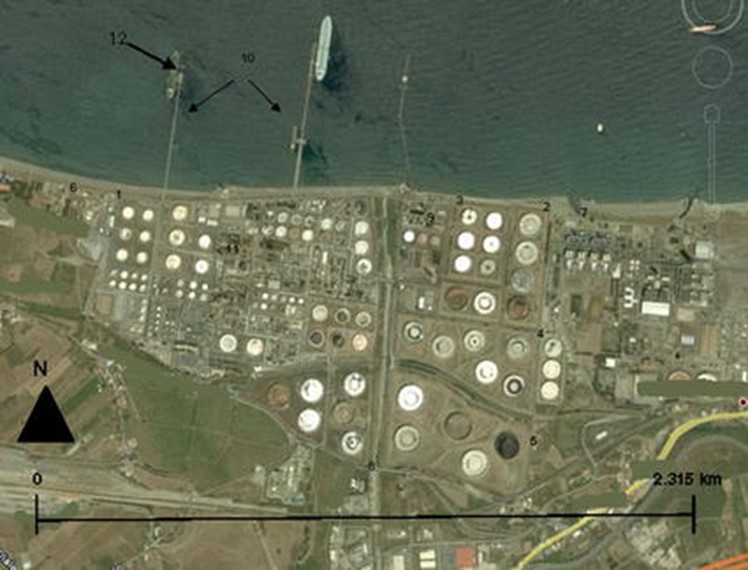
Figure 3. Tsunami impact scenarios at an oil refinery (Cruz et al., 2011)
Many clients may share the same off-site facilities. This may result in the complexity of resource management. There may be problems regarding the availability of assets, management of traffic, and scheduling of shipping.
Solutions provided by IT-based strategic management
ERP (Enterprise Resource Planning) consists of software packages – Terminal Logistics Suite and Oil Movement Suite. This will result in overall efficiency improvement. This will help in optimizing a combination of chemical products, route selection, and scheduling machinery. Systems concerning plant assets are integrated using ERP. In case of machinery breakdown, operations may be re-routed. Thus, there may be optimum utilization of machinery.
In case of an emergency or accident, the smart alarm system will get activated. ERP will help operators to simplify complex operations. Important operations will get priority. Because of the machinery tracking system, contamination will not be there. Overall, operators will have a safe working environment (Yokogawa, 2019)
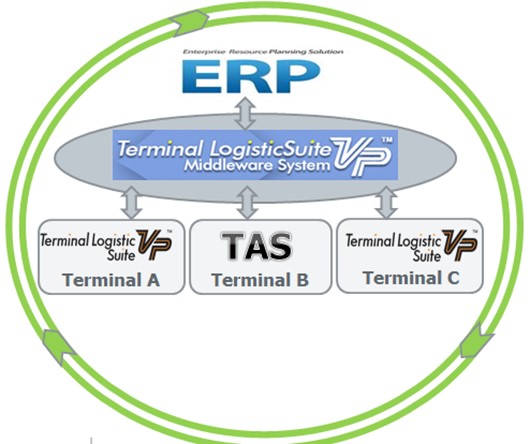
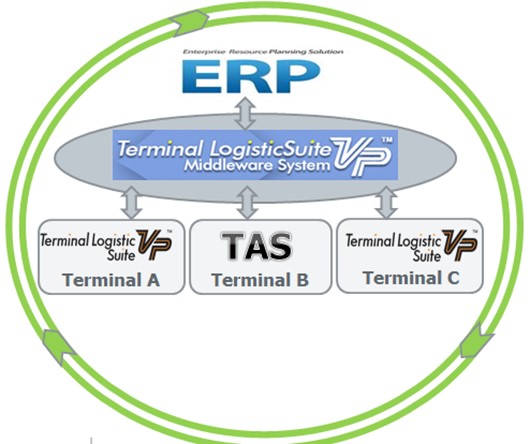
Figure 4. ERP implementation of Refinery Offsite Operations (Yokogawa, 2019)
Advantages for consumers/users in refinery offsite operations
Logistic problems can be addressed. Problems with vessel demurrage may also be handled. This will ensure timely delivery. Operations will be fast and precise. They can be recorded and tracked. Effective connectivity will be there for control and business process, for example, in payment receipt to receipt of the purchase orders. Improvement in quality and operational safety will reduce turnaround time (Yokogawa, 2019).
Reasons for better profit margin
Inventory and loading, and unloading data are maintained on a real-time basis. This helps in the context of optimization of refinery offsite operations. Now, operations are fast and precise. The probability of failure or error is less. For logistics, appropriate routes are selected. This leads to fewer line flushes. Contamination is not there. Business/operations sustainability is maintained due to utilizing real-time data concerning refinery offsite operations.
Quality control is maintained with the help of efficient data tracking. As the inventory data is real-time, it helps appropriate delivery, shipping, loading, etc. In addition, there is a run-time monitoring process for machinery/equipment. So, maintenance can be scheduled appropriately. Hence, machines/equipment functions well (Yokogawa, 2019).
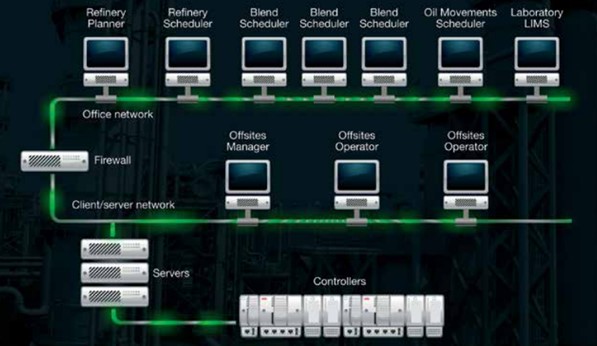
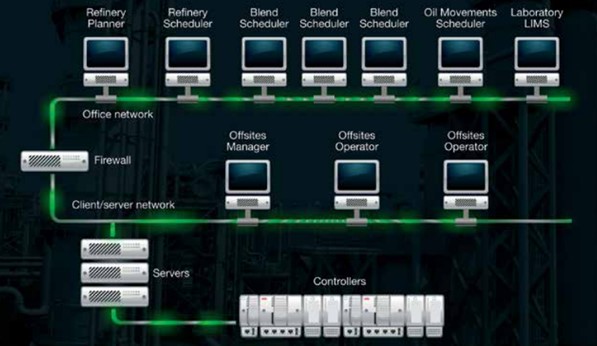
Figure 5. Connectivity of off-site staff with Refinery Planner and scheduler (ABB, 2013)
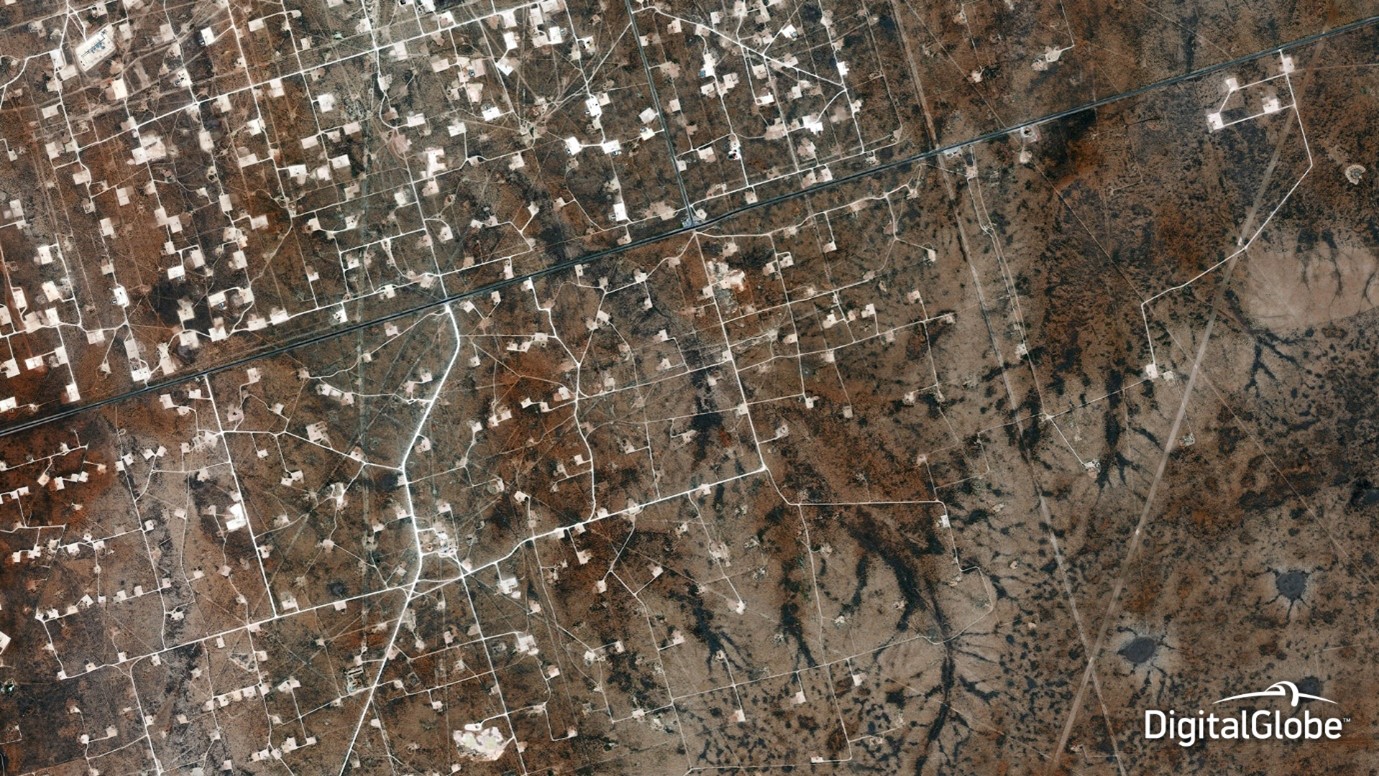
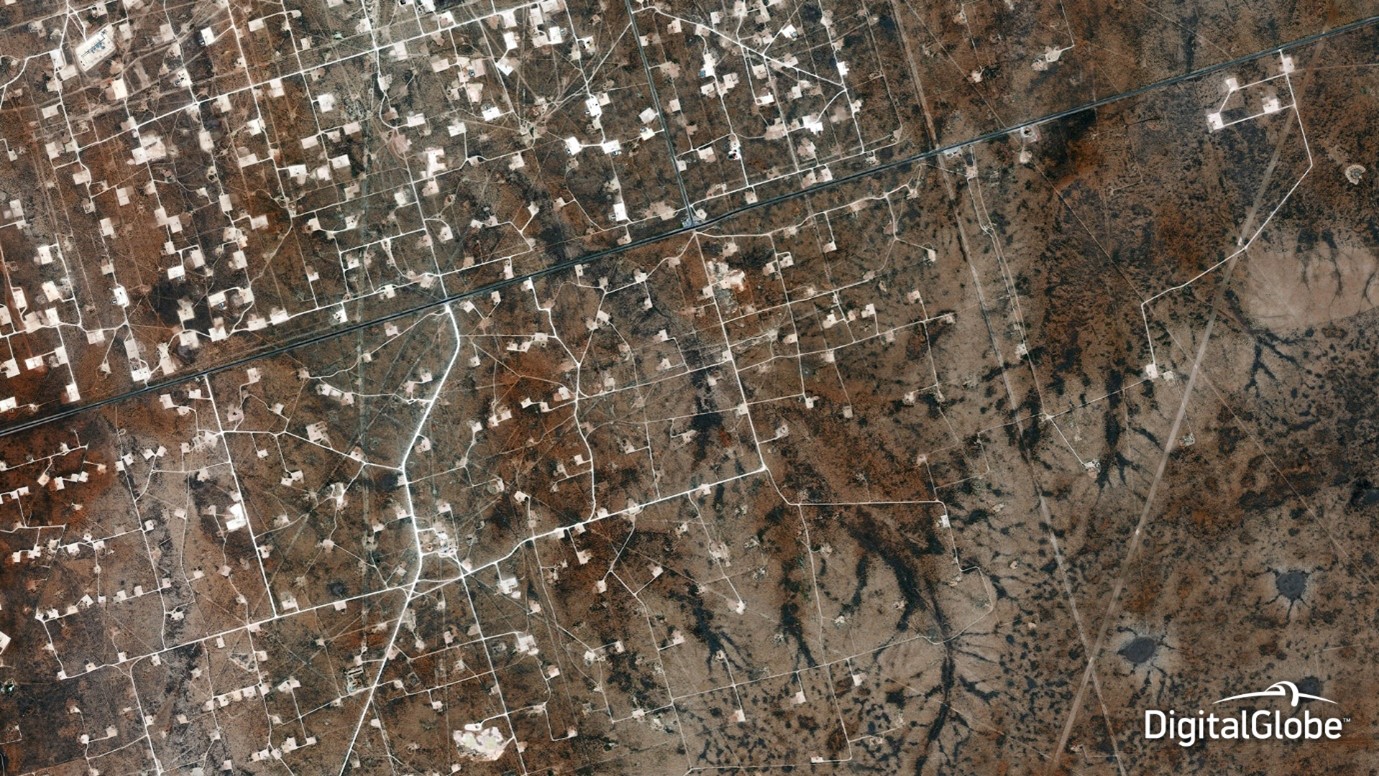
Figure 6. Oil and Gas Operational Sites concerning West Odessa Texas (United States)
References
- ABB. (2013). Oil Refinery Offsites Automation opportunities to improve profitability, https://library.e.abb.com/public/4f58f8c3879e9e19c1257b75003c525b/Oil%20Refinery%20Offsites.pdf, Accessed on November 22, 2019.
- Crude Oil Refining. (no date). https://za.pinterest.com/pin/205617539217980321/, Accessed on November 22, 2019.
- Cruz, A.M., Krausmann, E. & Franchello, G. Nat Hazards (2011) 58: 141. https://doi.org/10.1007/s11069-010-9655-x, https://link.springer.com/article/10.1007/s11069-010-9655-x, Accessed on November 22, 2019.
- Yokogawa. (2019). Off-site & Terminal Management, https://www.yokogawa.com/solutions/solutions/oprex/oprex-transformation/oprex-supply-chain-optimization/off-site-terminal-management/, Accessed on November 22, 2019.
#RefineryOffsiteOperation #RefineryOffsiteOperation #CrudeOilRefinery #In-PlantMaterialMovement #RefineryOnsiteOperation #TerminalOperations #TankFarmManagement #FuelProductsBlending #TerminalLogisticsSuite #OilMovementSuite #DataTrackingQualityControl
1 2 3 4 5 100%
1 2 3 4 5 0%
1 2 3 4 5 0%
1 2 3 4 5 0%
1 2 3 4 5 0%