Introduction
PEMEX Refinacion, Mexico awarded two lump-sum contracts in 1994 to ABB Industrial Systems, Inc., Houston for the engineering and implementation of an integrated advanced online blend control, optimization, and planning systems for its Cadereyta and Tula refineries. The detailed engineering for the blender is done by two local Mexican engineering companies, namely, CONIP Consultores y Contratistas for Cadereyta refinery and GMD for Tula refinery. ABB has implemented the identical state-of-the-art advanced online blend control, optimization, and planning systems in both PEMEX refineries.
This blog presents details of the ABB implemented blend control systems from its features and system architecture points of view.
Blender design
The design of blender in both PEMEX refineries has the following characteristics:
- Tank-to-tank in-line blending, using blending components from component storage. Most of the stock tanks in both refineries are closed during blending keeping their qualities constant during blending. However, few stock tanks are live or running during blending with considerable variation in their qualities
- The blending control system design allows for the use of up to 16 simultaneous blend components (expandable); it also handles the use of oxygenates such as MTBE and TAME, and additives -TEL, Aniline, and detergent.
- Stock qualities (RON, MON, %Ar, %Olef, RVP) are measured by one online NIR using multiple stream sampling systems. Each stream is sampled once every two minutes. Distillation points for the stock tanks are input from laboratory values.
- Blend product qualities are measured online by three analyzers, namely, NIR multi-property analyzer (RVP, RON, MON, %Ar, %Olef), multi-point chromatography distillation analyzer, and an RVP analyzer.
- Configured up to 8 grades (expandable) of unleaded gasoline, both leaded and unleaded, with multiple quality specs (RON, MON, RDOI, RVP, Distillation point).
- The maximum blender flow rate is 12,000 Bls/hr. The blender hardware architecture consists of a blender manifold for up to 16 components; the legs for each component include mass flow meters, control valves, strainers with pressure switches across it, pumps with computer-controlled recycles, and block valves.
NIR-type multi-property online analyzer for RON, MON, RVP, and distillation, mounted in an analyzer shelter system, which integrates together with the analyzers, the sampling system, and the prototype fuel system used by the Octane comparators. Compared with conventional analyzers, CC-96-124 the latest generation of Near Infra-Red (NIR) multi-property analyzers promise equal performance and more properties at a fraction of the operating and maintenance costs.
Control hierarchy levels
ABB’s blend control, optimization, and planning system consists of the following three distinct control levels:
- Regulatory Blend Control (RBC) – First level of blend control strategy resides in Fisher DCS ProVox and controls the amount of each component in the final product tank automatically. Although this level of computer does not give any guarantees to blend the product to specifications as it does not use any analyzer feedback, it does relieve the operator from monitoring the process continuously.
- Advanced Online Blend Control and Optimization (ABC) – The second level of the blend control strategy is a scheme that is implemented in the HP-9000/715 computer and is linked to Fisher ProVox executing the first level of control. This control uses the analyzers feedback, corrects the recipe frequently, and guarantees the final product on specifications. This is a very complex technology and the refineries achieve considerable economic benefits because of continuous optimization and feedback.
- Offline Optimization and Planning System (OOPS) – Third level of the blend control strategy is offline optimization of a blend recipe taking into account the refining process as expected in advance. This is done on an HP X-terminal by the refinery planner and then he downloads the optimized recipe to the online blend control (ABC) system for further online control and optimization and is finally executed in Fisher ProVox by RBC. The planner typically may plan many recipes at one time depending upon the refinery’s operational characteristics.
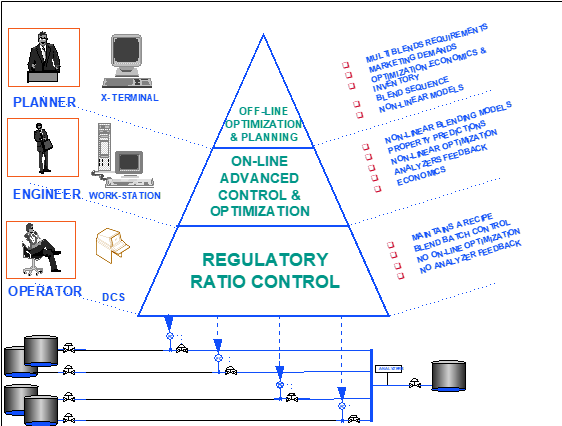
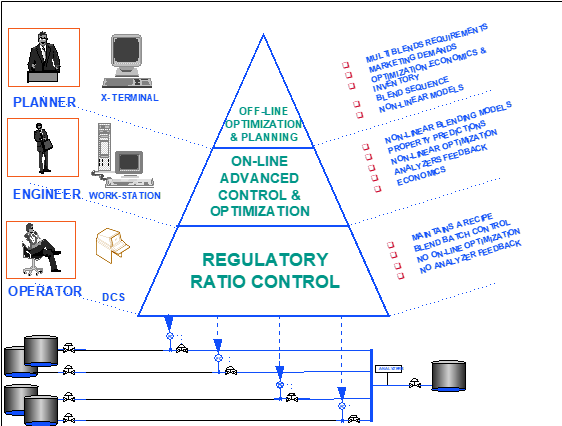
Figure 1. Hierarchy of ABB Blend Control System
Technology set
ABB Integrated Blend Control, Optimization, and Planning System is based on ABB or any third party vendor DCS for Regulatory Blend Control (RBC) and UNIX HP work-station for advanced on-line and off-line blend control, optimization, and planning system. It uses the technology set shown in Table 2.
Components of ABB blend control system technology set
- Runs Unix HP-UX 9.0+ multi-user, multi-tasking robust operating systems.
- SQLbase, ORACLE, or Interbase as Database Engines
- Graphical User Interface (GUI) based on SQL Windows, ORACLE Forms or BridgeBuilder on HP work-station
- Models for gasoline, distillates, and fuel oil blends.
- Non-linear Blending Models for gasoline blends
- User-selectable options for multiple Correlations for 36 qualities.
- 3 User-definable blend qualities
- EPA Simple and Complex Emissions Models for reformulated gasoline
- Generalized free-formatted linear and non-linear equations generation and management system (GAMS)
- Many user-selectable linear and non-linear equation solving and optimization algorithms
- Available algorithms: MINOS5, CONCOPT, DICOPT, CPLEX, LAMPS, OSL
- Multi products, Blends, and Multi-periods
- Stock Pooling and calculation of composition and properties.
- Calculations of average qualities for a set of blends.
- Roll-over of blend planning periods
- Computer gateway to third-party vendor DCS, such as Honeywell TDC-3000, Foxboro, Yokogawa, etc.
- Tank Gauging and Inventory Management System
- Laboratory Information System
- Refinery Information System
Integration
ABB integrated blend control, optimization, and planning systems consist of many other sub-modules besides the hierarchical control levels to provide many support functions. These sub-modules are:
- Tanks Information Management System
- Laboratory Management System
- Comprehensive Reports management System
- Component Properties Management System
- Blends Information Management System
- Online Blend Control and Optimization Simulation
These modules are integrated in a seamless manner and represented in Figure 2.
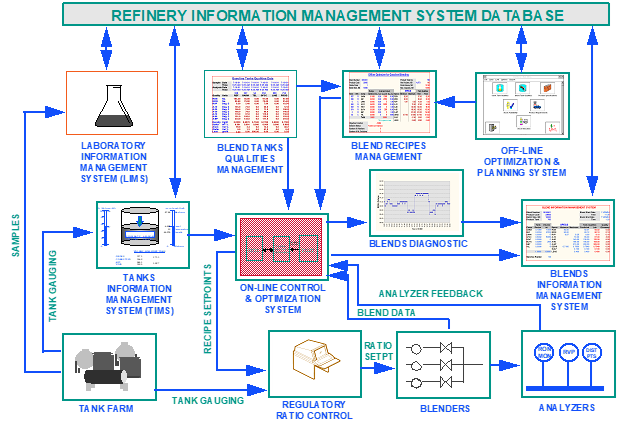
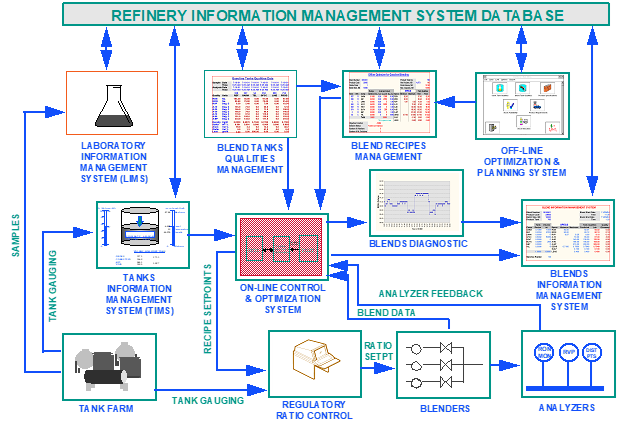
Figure 2. ABB Integrated Blend Control, Optimization, and Planning System
The ABB Integrated blend control, optimization, and planning system is consistent from off-line blend optimization and planning system to on-line blend control and optimization in using the same blend models and correlation and non-linear optimization algorithms. The off-line blend optimization and planning system has online access to stock and blend properties, tanks inventory, and updated model biases to plan the next blend recipe as close as possible to final specifications.
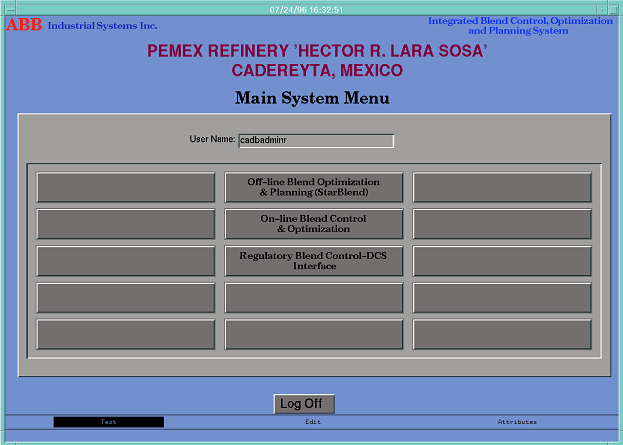
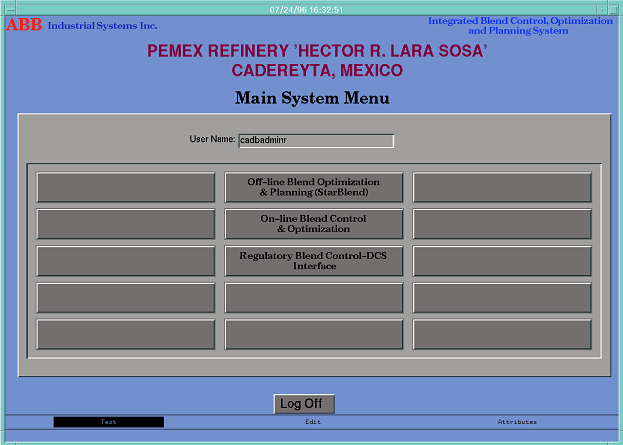
Figure 3. Main Systems Access Display
Figure 4 shows that all ABB Blend control, optimization, and planning system modules are accessed from one display. The DCS-RBC Interface shows all data communication between RBC and advanced control on a workstation.
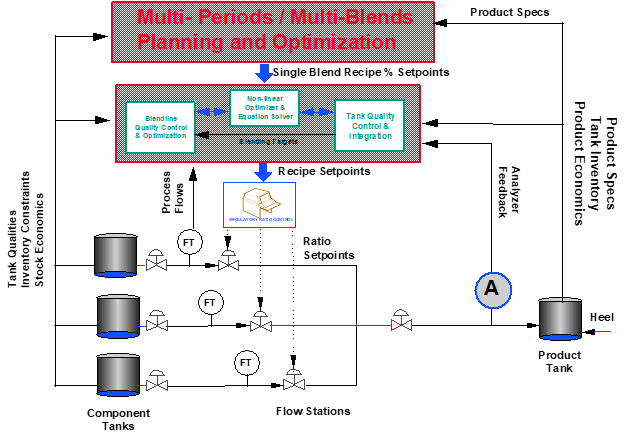
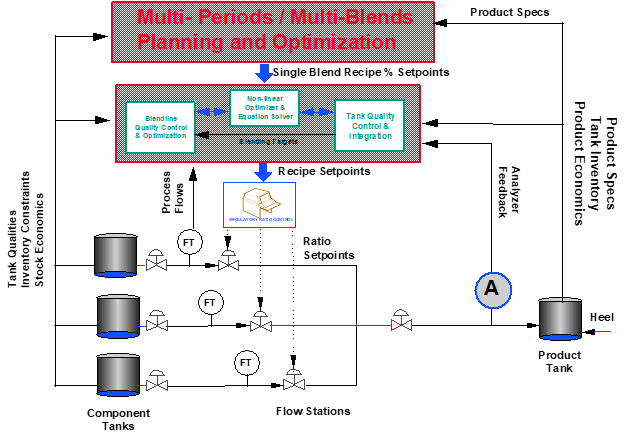
Figure 4. ABB Blender Architecture
The refinery planner either optimizes a single blend for the next execution or uses a 15 days rolling period plan scheme to optimize the next blend. The input data for stock qualities, blend tanks qualities, stock, and product tanks inventory, etc. are either manually entered for case studies or retrieved automatically, at the user option, from the online process database. After the planner reviews the next recipe, he can download it to the blend operator and online control for execution. Figure 5 shows a typical rolling period that blends the planning cycle.
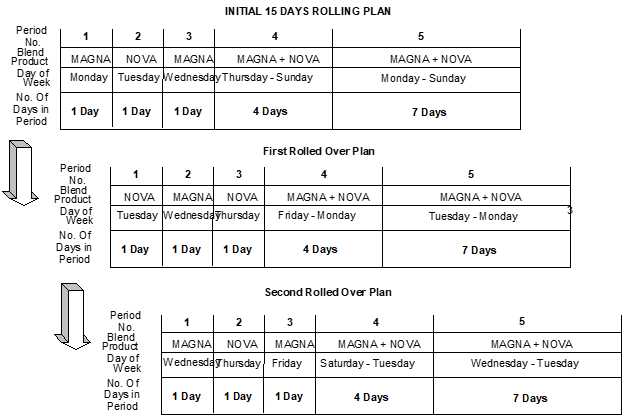
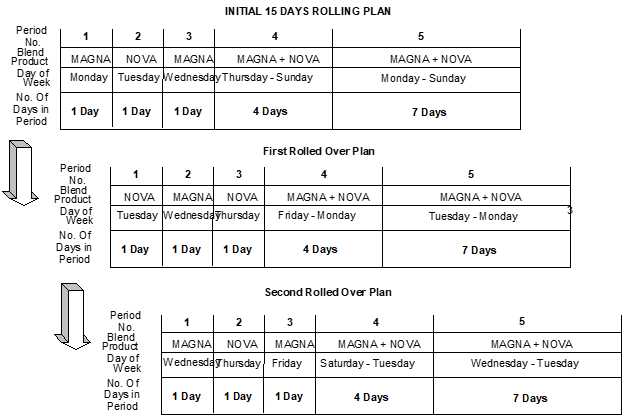
Figure 5. A Typical Rolling Period Blends Planning Cycle
After the next recipe is downloaded to DCS and the online control system, the blend is started from the Regulatory Blend Control (RBC) in DCS. RBC is responsible for the checking of data for auto blend line-up and pumps selection and blend start-up process, including ramping and pumps start-up process. The RBC Blend operator follows a sequence of operations to select a blend recipe as downloaded from the planner to finally start the blend with one start/stop toggle switch. The blend sequence in RBC is shown in Figure 6.
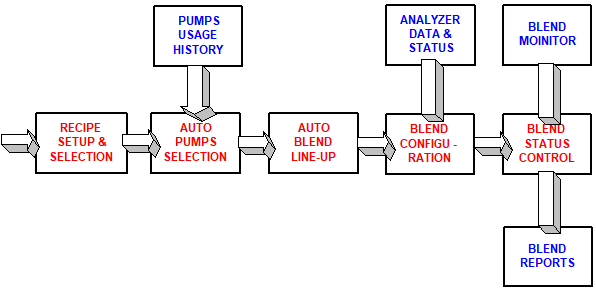
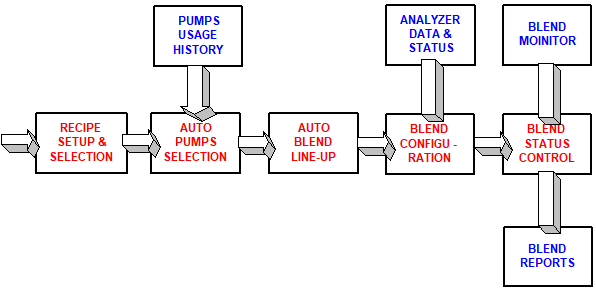
Figure 6. RBC Path and Sequence
The online blend control and optimization system on the HP workstation starts the control after the total blend volume has reached a preset initial volume to allow time for the analyzer to stabilize and ensure the start of the blend. This process is fully automatic and does not require any intervention from an operator or blend engineer. The online blend control and optimization system has a number of displays for monitoring the online blend control and optimization and presents very comprehensive and complete information about the current blend in execution. Figure 7 shows the path for online blend control and optimization displays.
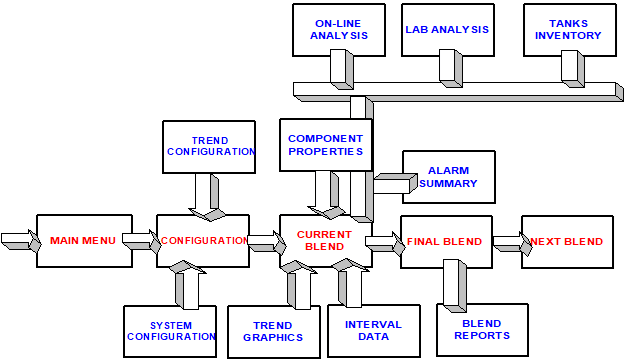
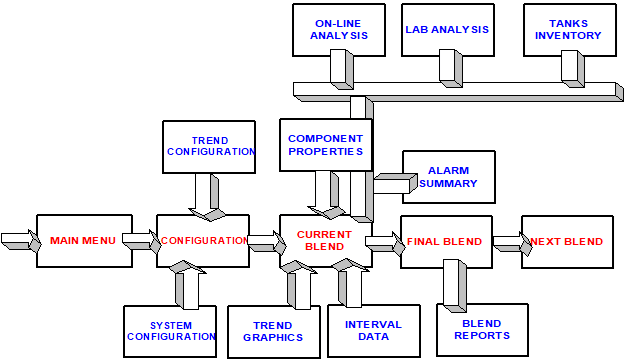
Figure 7. Display Path for Online Blend Control and Optimization
The online blend control and optimization system is finally shut down by the shut-down sequence in RBC and issues a final blend report. Additionally, all final blend information is also sent to the blends information management database and can be queried for any final blend information online. The final blend report is very comprehensive and integrates the final lab analysis of the blend to show any giveaways. The final blend report can be used as blend certifications. Figure 8 shows the flow of information from planning to the actual execution of a blend. The next sections in this blog present the salient features of all control levels of ABB’s integrated blend control, optimization, and planning systems implemented at two of PEMEX refineries.
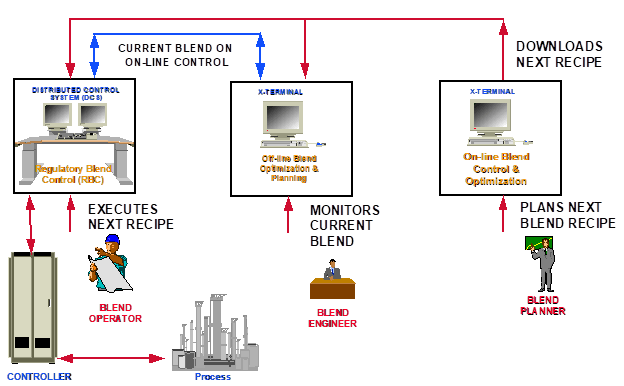
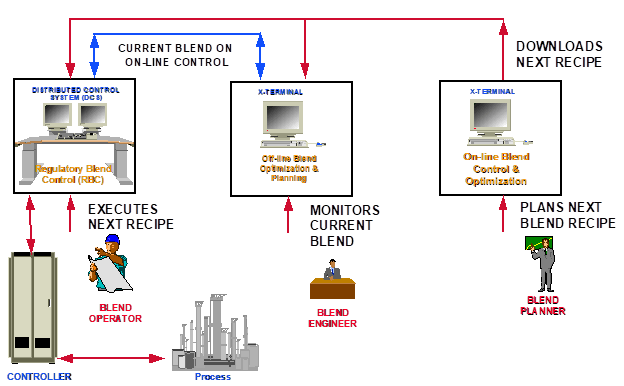
Figure 8. A Complete Blend Planning, online Control, and Optimization Cycle
Control level – RBC
The Regulatory Blend Controller (RBC) works through standard PID flow control loops by reading digital values and flows from the loops and downloading setpoints to the loops. In general, the setpoints to the RBC are percents of each component, a total rate, and a target amount; and its outputs are a set of flow control setpoints as shown in Figure 9.
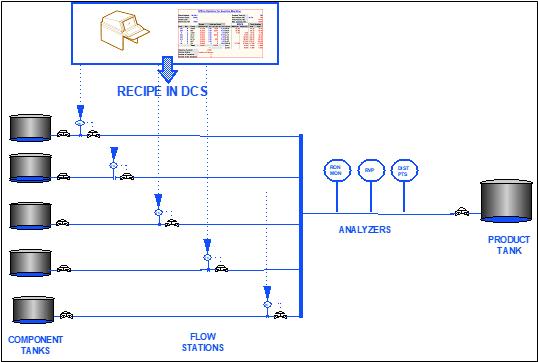
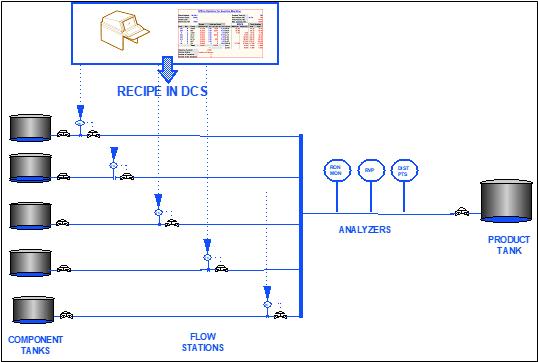
Figure 9. Regulatory Blend Control (RBC)
The Regulatory Blend Control (RBC):
- Downloads setpoints to
- Maintain flow ratios to match a given recipe;
- Maintain a target total flow rate for the sum of all component flows;
- Ramp when appropriate;
- Totalizes the amount of each stock;
- Displays the target blend amount and the anticipated amount usage of each stock;
- Starts to blend on a START command.
The RBC is capable of independently executing a complete blend without the advanced blend controller or online product analyzers. However, it has no feedback for the product quality and therefore blends only for the recipe ratio setpoints.
The following sections describe the features of ABB’s Regulatory Blend Control (RBC) in DCS.
- Recipe Selection
- LOCAL/AUTO/REMOTE Recipe Sources
- Recipe Normalization
- Pump Usage History
- Auto Pump Selection
- Auto-Blend Line-up
- Blend Status Control
- Ramping
- Pacing
- Timing
- Amount Monitoring and Control including additives
- Other Monitoring Features such as tanks gauging and blend analyzers
- Current Blend Status Screen Report
- End-of-Blend Screen Report
Figure 10 shows a typical RBC display for the auto-lineup of pumps and tanks for the blending operation. This display enables the operator to view either the current or the next blend line-up sequence.
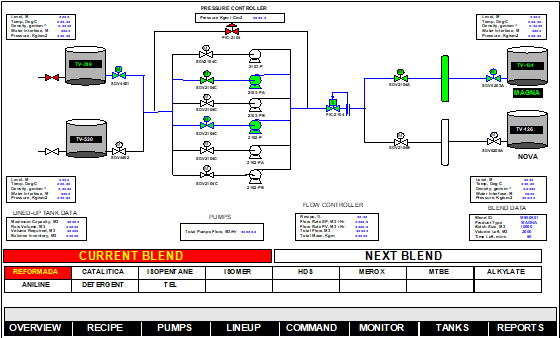
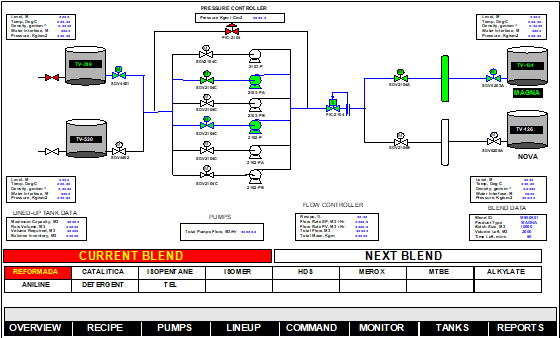
Figure 10. Auto-Blend Line-up Display
Advanced online blend control and optimization system
ABB Industrial Systems, Inc.’s online blend control and optimization system is an advanced control program that uses non-linear blend models and non-linear equation solvers and optimizers. The system is based on the StarBlend™ technology developed by Texaco for gasoline, distillates, and fuel oil blends. The online blend control and optimization system interfaces with offline planning and optimization system using the same blend models and mathematical algorithms. It allows flexibility in specifications and requirements to meet individual refinery needs of online blend control and optimization. The system is written in FORTRAN and runs in a UNIX workstation environment connected to the user’s DCS through a new or existing supervisory information system in an HP workstation. The blending data is contained in a relational database designed to integrate with a plant-wide database system.
Figure 11 shows the information flow diagram for the ABB’s advanced online blend control and optimization system.
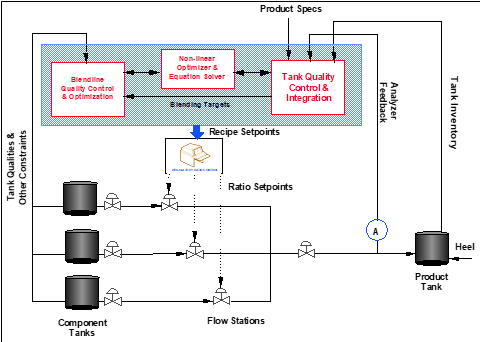
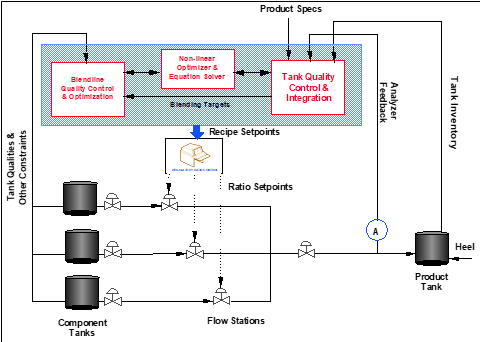
Figure 11. Advanced Online Blend Control & Optimization
The optimal controller works in conjunction with a regulatory control system. The optimal controller continuously calculates the economic optimum recipe to move the tank qualities to their targets and then keep them on target. The advanced online blend control and optimization system uses the following data through system interfaces:
- Current component qualities measured either by online analyzers or by lab analysis of frequently taken samples of stock tanks and is used in feed-forward prediction of blend-line qualities;
- Current and cumulative component flows from each control stations to calculate the predicted blend-line and product tank qualities respectively;
- Blend-line qualities measure by online analyzers for feedback control and model error corrections.
Based on the above data, the online control system predicts the blend-line and product tank qualities by using the non-linear blend quality models corrected for errors by using the continuous dynamic feedback of error correction factor, bias. The tank quality integration is done again using the same non-linear blend models and solving the non-linear set of equations for the last calculated tank qualities and additional blend-line calculated accumulated in execution cycle time. The non-linear set of equations for the tank integration are solved by the non-linear optimizer MINOS™.
The currently integrated tank qualities are compared with the final target specifications and quality targets are back-calculated for blend-line. The recipe control module of the system then optimizes the component ratios or recipes by using an objective function of maximum profit or minimum quality giveaway and minimum deviation from the preferred recipe.
Tank quality integration is done more often, for example, every 4 minutes, and the recipe optimization is done after 7-8 runs of tank quality integration. This strategy keeps track of what is in the product tank and how best to blend further not only to produce the tank on specifications but also with minimum quality giveaways.
The optimization takes into account the cost of inventory, cost of giveaways and violations, cost of stocks, and price of products to come up online with optimum ratios of components to blend to specifications.
The critical factor in the online blend control and optimization system is the qualities of components and online analysis of blend-line. If the component qualities are changing while blending due to direct run-downs from the units, their qualities must be analyzed either by online analyzers or made available by laboratory analysis of frequently taken stock tank samples.
ABB’s advanced online blend control and optimization system is resident on a RISC-based HP work-station using UNIX as the operating system. There are a number of user displays that provide useful information about the results of non-linear optimization of recipes and tank quality integration calculations which are executed cyclically in the background.
The online blend control and optimization system interacts with the blend operator and/or engineer through the following displays access menu as shown in Figure 12. This figure shows the flow of information and road map to GUI displays for ABB online blend control and optimization system.
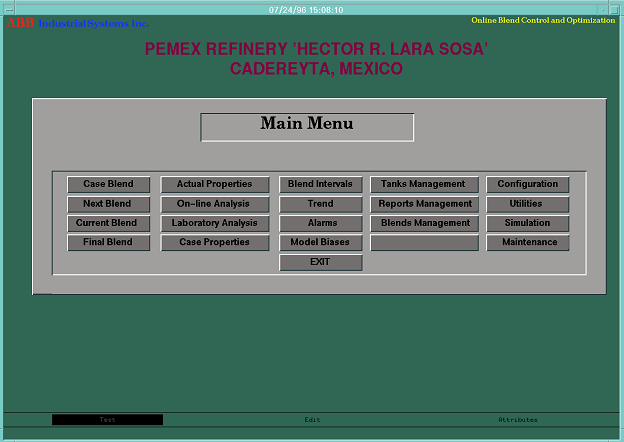
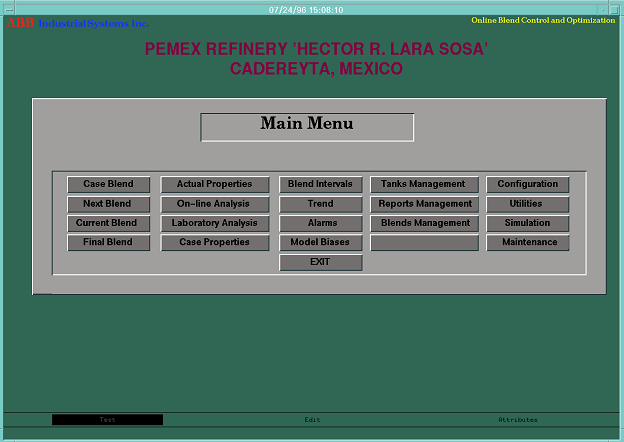
Figure 12. Main System Access Menu
Offline blend optimization and control system
StarBlend™ offline optimization and planning system is a decision support tool that produces optimal blend recipes for gasoline, distillates, and fuel oils. The system is designed to assist the refinery’s planning group to reconcile current daily conditions and shipping requirements with monthly production targets.StarBlend™ is a state-of-the-art system for the offline optimization and planning of gasoline (including reformulated), distillates, and fuel oil blends. The system basically comprises of
- Relational Database Manager (RDBMS) such as Interbase™ on HP-workstation;
- Graphical user interface such as Bridgebuilder™;
- Linear and non-linear Blend Models for all types of blend products;
- General Algebraic Equations Management System such as GAMS™
- Non-linear optimization algorithms such as MINOS™
Figure 13 shows the representative diagram for the StarBlend™ offline blend optimization and planning system.
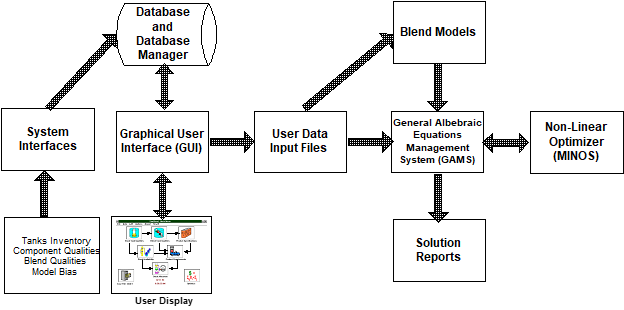
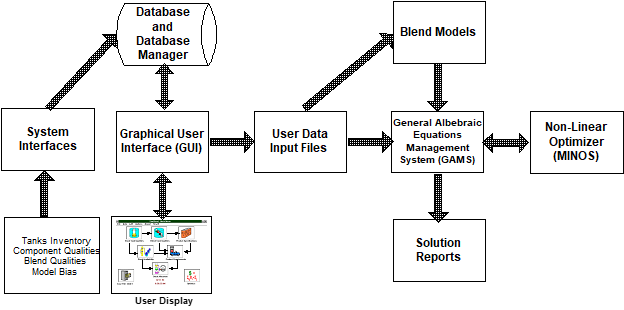
Figure 13. System Architect for StarBlend™
ABB’s offline blend optimization and planning system uses TEXACO’s StarBlend™ System. ABB has ported this system to the RICS based HP work-station using the HP-UX operating system. Figure 14 shows the main display for accessing the offline blend optimization and planning system.
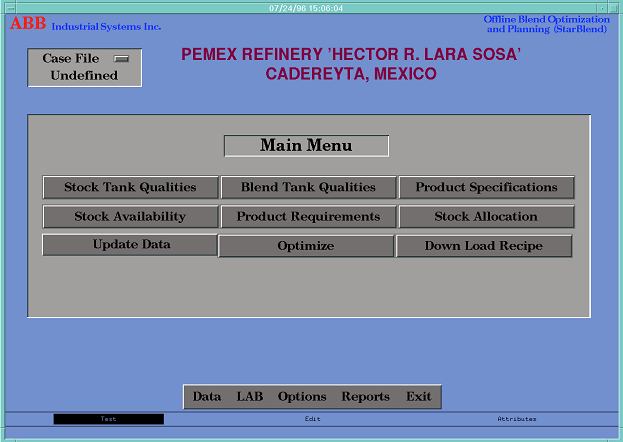
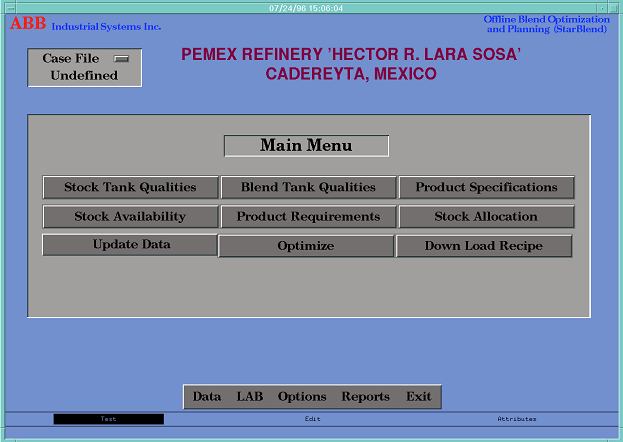
Figure 14. Offline Blends Optimization and Planning System
StarBlend™ is a spreadsheet-like and SQL-based decision support tool developed by Texaco Refining and Marketing, Inc., and produces optimal stock allocations between multiple time periods with on-spec blend recipes for gasoline, distillates, and fuel oils. ABB provides a version of StarBlend™ which is
- Customized for client’s off-line planning and scheduling requirements.
- Installed on customer’s platforms such as 486+ PC, HP workstation, etc.
- Integrated with advanced online blend control and optimization module.
- Integrated with tanks inventory management and laboratory information systems for the latest information to be used in optimization.
StarBlend™ is a comprehensive program allowing flexibility in specifications and requirements to meet an individual refinery’s needs. It is a standard product software (only PC version) that is proven, reliable, and can be immediately used. It has virtually no restrictions (subject to computer memory size) on the number of time periods, number of products, number of product property specifications, number of components, and inventory configurations to configure the refinery’s unique supply and demand situation. Its enhanced options allow direct interface with the Laboratory Information System and tuning of proven nonlinear property prediction models to your plant data. Its usage extends to the blending of all grades of gasoline, middle distillates, and fuel oils.
Optimum batch volumes and blend recipes for multiple time periods are generated based upon feedstock production and properties and finished product shipping requirements and quantities to reconcile (if required) with monthly planning targets, and with the desired features and capabilities of:
- True non-linear optimization with the maximum profit or minimum giveaway objective along with adherence to the preferred recipe. Infeasibilities are avoided by allowing the buying/selling of components and qualities if necessary.
- Multi-period planning with inventory control constraints.
- Blending a full range of gasoline grades, aviation jet to diesel fuel for distillate blends, and fuel oil blends.
- User-selectable built-in well-proven correlations for over 40 properties (e.g. Octane, RVP, Volatility, Aromatics, Oxygenated stock, Cetane number, Freeze point, Viscosity, Sulfur, etc.)
- Allowing user-developed property correlations.
- Individual fine-tuning of correlated properties with biases to fine-tune models to plant operations.
- Pooling of plant components.
- Laboratory and tank data download interface.
- Easy access to model data and results via spreadsheet and window format.
- The number of multiple time periods, feedstock components, and product grades limited only by computer memory size availability.
- Choice of units (Metric/US).
Computing platform
The blending software is completely resident in the HP 9000/715 workstation. Various components of an integrated blend control, optimization, and scheduling system reside in different computing components. The central place for data communications is a relational database management system (RDBMS) and various interfaces communicate data from various systems to RDBMS and vice versa.
Figure 15 shows all system components and their resident computing platforms. The planner’s blending off-line optimization and planning system is resident in the HP workstation and accessed by X terminal. The online control and optimization, the various databases such as the component tank qualities, component stock inventory, component prices, product specs, blending recipe, field equipment lineup, and the various report archives and history are resident on the work-station. The Fisher DCS runs the actual blend ratio control, and the blend MOV and pump startup and shutdown sequence control. It also interfaces to the mechanical blender manifold equipment (control valves, turbine meters, analyzer(s)), the MOV’s for blend component tank lineup, and remote control of component pumps. The operator man-machine interface for RBC is on 2 Fisher ProVox consoles (redundancy for reliability), each capable of displaying all the information needed to set up, run, and monitor the blend, including inventory and lab data. The online blend control and optimization man-machine interface is a UNIX X-terminal.
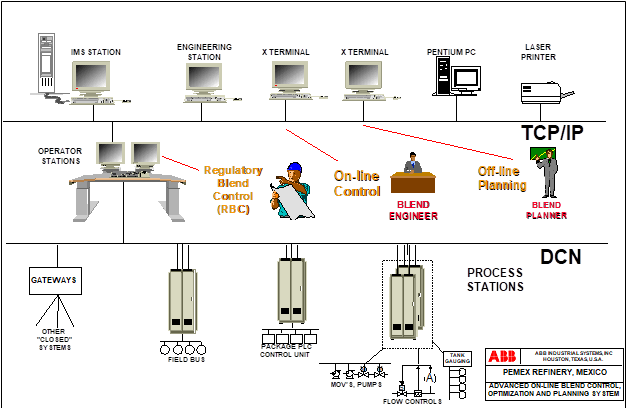
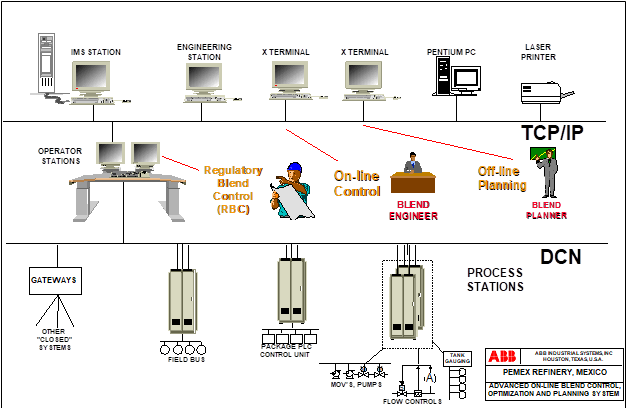
Figure 15. System Architecture
Conclusion
ABB has implemented successfully state-of-the-art advanced online blend control, optimization, and planning systems in two Mexican refineries. This system has helped PEMEX to modernize its refineries and bring them to par with the best plants in the world today.
#ComprehensiveReportsManagementSystem #Off-LineBlendOptimization #On-LineBlendOptimization #GasolineBlending #Non-LinearBlendingOptimization #LinearBlendingOptimization #LaboratoryInformationSystem #Non-LinearBlendModels #LinearBlendModels #GuiBlendControl
1 2 3 4 5 100%
1 2 3 4 5 0%
1 2 3 4 5 0%
1 2 3 4 5 0%
1 2 3 4 5 0%