Introduction
In today’s global economy of fluctuating crude oil prices, the worldwide refining industry is struggling. Costs are rising while refining volumes are decreasing. High fuel prices in recent years have reduced its global use, resulting in an oversupply of reserves. As a result, the volumes of crude oil being refined have decreased. The diminished refining volumes become a critical issue for countries with government-controlled fuel and crude oil prices.
Efficient and economic fuel blending then becomes an attractive source of revenue to minimize these refinery losses and improve the bottom line. For example, a conservative saving of $0.10/Bls gasoline (the industry average is $0.20-0.30/Bls) will save $1.6 – 2.0M/year for a refinery producing 100 kb/day with 45-55% conversion to gasoline production.
But starting a blending project is a complicated endeavor, one that can be problematic and can easily fail if not properly managed. Fuels blending projects require strategic management and specialized technology to ensure success and enable a refinery to realize savings and renewed revenue.
In this blog, we will discuss the technological and management aspects of all required and desired components of a typical fuels blending system in a refinery and enumerate their inherent problems and brief solutions to overcome them. A detailed discussion of this topic will be presented by the author in a 3 days’ comprehensive public course on May-19-21 in Mumbai, India. Further information about this seminar is given in this journal or also be obtained on the website www.globaloms.comMumbai.
A typical fuels blending system
A typical fuel (gasoline, diesel, fuel oils) blending system consists of the following components:
- Tank farm
- Tank Gauging System
- Lab Analysis
- Field equipment
- Additive controls
- Online Analyzers
- Distributed Control System (DCS)
- Advanced Control And Optimization Software System
- Blend header
- Product dispatch system
Figure-1 shows the integration of the above-mentioned modules in a typical refinery fuel blending system.
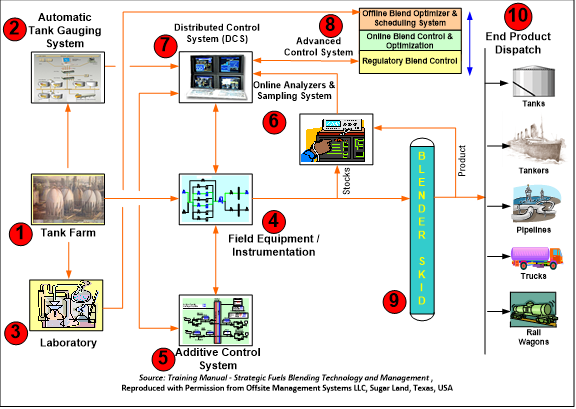
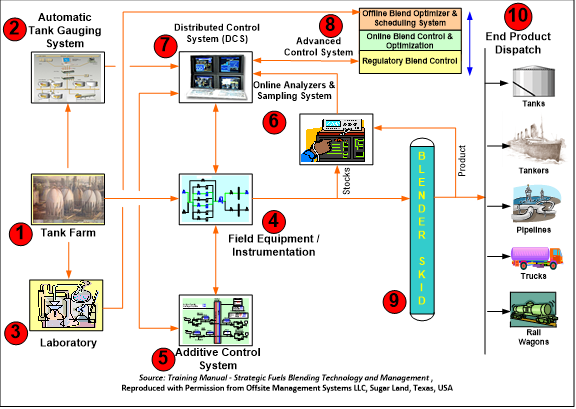
Figure 1. Modules of a Typical Fuels Blending System
One of the most important aspects, not shown distinctly in the above figure, is the complexity of blending models which can be the cause of blending problems if they are not properly formulated and configured. Next, we will divide the discussion in the next paragraphs into two areas, namely, technology and management for a balanced perspective of a blending system.
The discussion on the technical aspect will revolve around problems, challenges, and opportunities for each of the modules represented in figure-1.
Tank farm
There can be as many as 300+ tanks for all feeds and products in a large capacity (300KB/day) refinery and only 30-40 of these tanks may be assigned to fuels blending operations. These fuel blending tanks may not be sufficient for a particular refinery and cause the following problems.
- Inadequate number of blending component tanks
- Excessive feeds streams used for blending
- Component tanks may not be closed during blending
- Only one or sometimes no tank available for any blending component
- Excessive product movement due to inadequate number of product tanks
The number of control loops and number of components tanks may not be the same
There are a number of methods to eliminate or minimize the above tank farm problems. They are, for example, stream pooling, proper planning to close component tanks during blending, minimizing the number of control loops, etc.
Tank gauging system
An automatic gauging system (ATG), to measure tank levels, is very essential for the efficient operation of a refinery as it calculates the tank inventory just-in-time during product movement from to and from the tank. Additionally, other tank measurements such as pressure, temperature, density, and water levels are also necessary for safety, custody transfer, and minimizing the water contents in final fuel products. Plants that do not have ATG installed face some of the following problems:
- Delayed tank inventory determination, hence problematic loading and unloading operations and fear of tanks spills and explosives accidents
- A dispute in custody transfer especially in crude feeds
- Inefficient blending operations
- The excessive manpower requirement to measure levels manually
Lab analysis
To meet the final fuel product specifications, one must know the qualities of components and product tanks. These are determined only manually in the refinery laboratory by taking an enormous number of tank samples. Sometimes, the analysis of these tank qualities takes 8-10 hours to get results. This delay in the availability of results put the refinery planner, blending engineer in waiting modes to plan and execute the blending recipe.
Some of the possible and successfully implemented solutions are online analyzers alone or in combination with the recent development of a model-based tank quality tracking system, saving millions of $ for the refinery from less dependence on the lab analysis and minimized involvement of the man-power.
Field Equipment
The blending system requires manual valves, motor-operated valves (MOV), flow measurement and controllers, pumps, and pressure controllers to operate and control the blending operations. Although the blending operation does not have a life-threatening situation, it can cause financial havoc for the refinery in terms of delayed product dispatch, product contaminations, burnt-up pumps, etc., if the field equipment is not designed and installed properly further lacking any blending automation.
Online analyzers
Online analyzers are implemented to eliminate some of the delayed availability of results from the lab analysis and provide near real-time the qualities of components and/or final blended product from the blend header depending upon the refinery’s specific extent of implementation. Although the technology has advanced a lot to analyze online multiple qualities by using spectrum-based multi qualities analyzers (NIR, NMR), they still inherit the problem of providing only online analysis. Refinery planners still have to rely on the lab analysis of blending component tanks to plan the next blend recipe, again a time-delayed process.
A recent advancement using the model-based tank quality tracking system (gomsTQTS™) and strategic placements of the online analyzers offer online tank qualities both in online and offline modes for 24 hours of the day. This technology saves refinery between 2-3MUS$/year from savings in laboratory manpower and makes qualities available just-in-time for blending purposes.
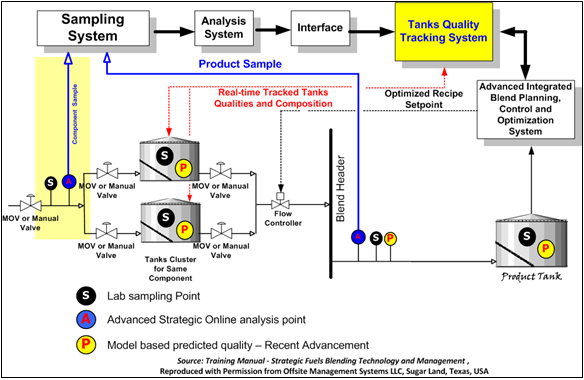
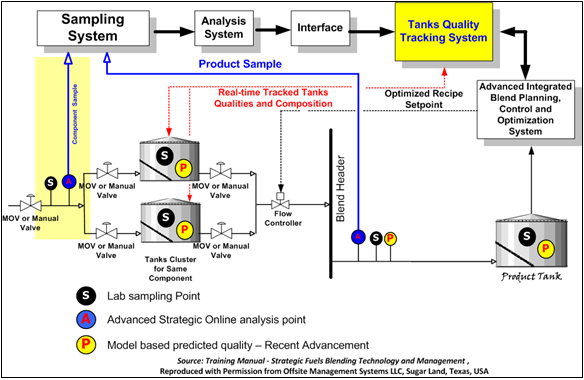
Figure 2. Strategic Implementation of model-based tank quality tracking system
Blending models
One of the most important aspects of blending technology is the blending models. Over the last 20 years, the blending components for the fuels have become more complex and interacting and they defy the simple linear blending equations. Thus the prediction of final blend quality has been a challenge as these components interact and thus change the final quality obtained simply by linear algebraic laws. If we take octane, for example, the complex interaction of components can either “penalize” or “boost” the final blend octane.
Examples of linear and non-linear models are as follows:
Where the term “f” in the above equation accounts for the complex interaction among blending components and can be estimated in a number of ways, too detailed to mention here in this brief article but is discussed at great length in the seminar by the author.
Distributed Control System (DCS)
This computer is the lowest level of control in the blending automation hierarchy and its purpose is mainly safety of the operation as well as to provide the ratio control of the blend components. The flow ratio of each component is maintained at a constant flow rate and can be changed only manually by the operator. The ratio setpoints are determined by the planner’s blend recipe and do not account for the online interaction of the components. There is no guarantee that the final blend will be on spec or quality will be given away. Hence, this level of control also has inherent “Trim Control” to correct the violation or quality give away of the product.
Advanced control and optimization system
DCS is good enough for blending control when the component qualities are constant and do not change during the blending. This was desirable but not practical in the majority of refineries that were designed with constraints of land and capital. Hence, the component tanks feed during the blending, that is, their qualities change constantly during the blend. This caused a big problem to control the final blend product quality as components interacted among them to alter significantly their blended property.
So, there was needed a way to change the component recipe constantly per their quality to keep the final product qualities within specs. This need gave rise to implementing the second level of control on top of DCS control which would alter the component setpoints based on the mathematical formulation of the blending equation. This is called advanced online blend control. This level of control not only controls the final product specs but also minimizes the cost of production by optimizing the ratio of components. Refineries were able to save 6-8MUS$/year by the implementation of the second level of the advanced online blend control system.
Now, there came the needs of the refinery planner. Till then they were formulating the blend recipe using rudimentary linear blend model-based recipe planning tools and would instruct the operator to make the blend based on this recipe. Naturally, blends either violated in specs requiring reblends or compromised the dispatch by quality giveaways. The development and commercial availability of offline blending optimizers came to the planner’s rescue and gave them sophisticated tools to plan and optimize the recipe to download for the online executions. This was such a success that the payback period of installing such a system was only a few months.
The next stage was focused on the reconciliation of blend models and input data between offline and online blend control and optimization to ensure that they used the same basis. Sometimes it was not easy if two levels of control systems were procured from two different vendors using different technologies for the blend models and blend optimization. Again, this is covered more in detail in the 3-day seminar by the author.
Figure-3 shows three tiers of advanced control and optimization system for fuel blending in a modern and automated refinery.
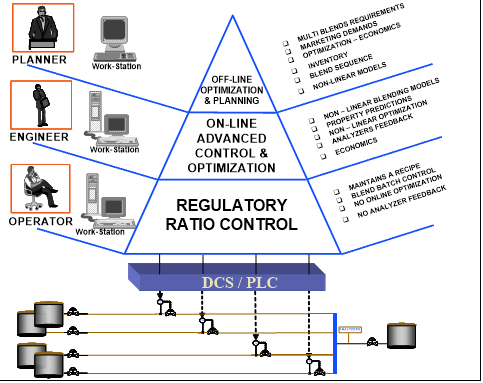
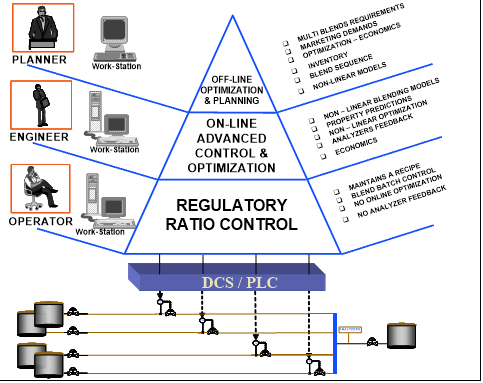
Figure 3. Three-tier Advanced Blend Control and Optimization System
Assessment of a blending system
A refinery blending manager is always perplexed by the following questions:
- Are re-blends and quality giveaways minimized?
- Are blends profitable?
- What is the payback for additional automation?
- How does our blending performance compare to other refineries?
The refinery seeks the answers to these questions either by using in-house expertise or hiring external consultants to evaluate the refinery blending system and recommend to the refinery management to consider a blending upgrade project. Each of the resources uses its own methodology to justify the investment by the refinery in a blending upgrade project.
The author of this article has developed a methodology that is general yet detailed enough to analyze all automation islands of the blending system in a refinery, determine the extent of investment required for upgrades, be able to compare the refinery’s blending system with other refineries in the world and also post-audit the blending project to verify the benefits claimed and justify the investment.
This methodology centers around two indices; namely, the automation effectiveness index and the operational efficiency index. The effectiveness index measures the suitability of each and every piece of equipment, tank farm, analyzers, computer systems, and lab analysis. The efficiency index, on other hand, analyzes the current method of blending in the refinery and determines its potential to be an ultimate fully automated blending system.
Figure-4 shows these two indices for a studied refinery and demonstrates the usefulness of these indices to determine the current blending state and required investment to upgrade to a fully automated system.
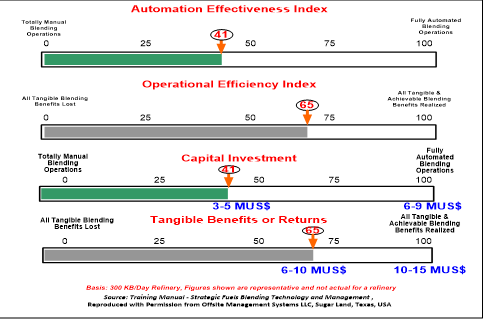
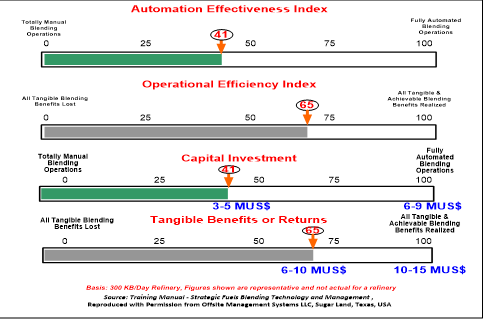
Figure 4. Correlations between Effectiveness/Efficiency indices
and capital investment/tangible benefits
If this analysis is performed for all refineries that a particular corporation owns, it can show the relative state of the blending systems of each of its refineries by ranking two indices as shown in figure-5. The two indices method can also be used to compare all worldwide refineries using the same consistent method.
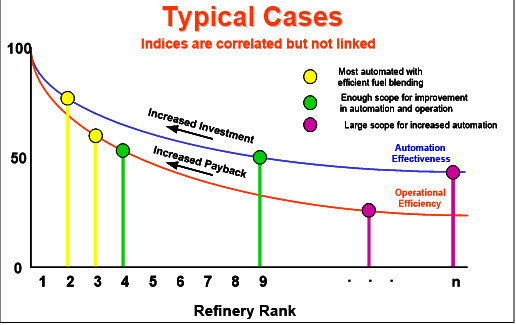
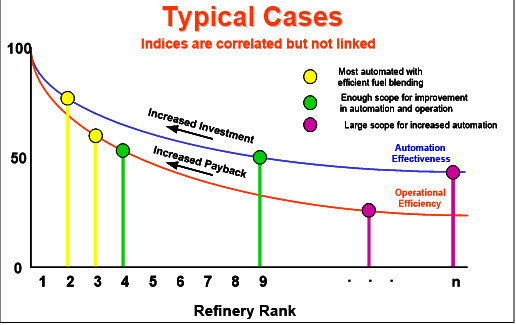
Figure 5. Relative ranking of blending system using the performance indices
Implementation of a blending system
It is not very uncommon in refining which is considering the upgrade and revamp of the blending project to try to allocate 6-10 M$ for the capital investment before going ahead with the project. The blending project upgrade is then, more often than not, put on hold ignoring and losing millions $ from the quality giveaway and reblends due to specs violation every year. Therefore, it is a better strategy to adopt the “pay as you go” implementation of blending automation components. In this respect, offline optimization is the fastest tool to implement at a low cost to achieve maximum benefits in a short period.
Figure-6 shows a blend of typical project implementation schedules using the strategy “pay as you go” and indicates ROI and Cost along the project timeline.
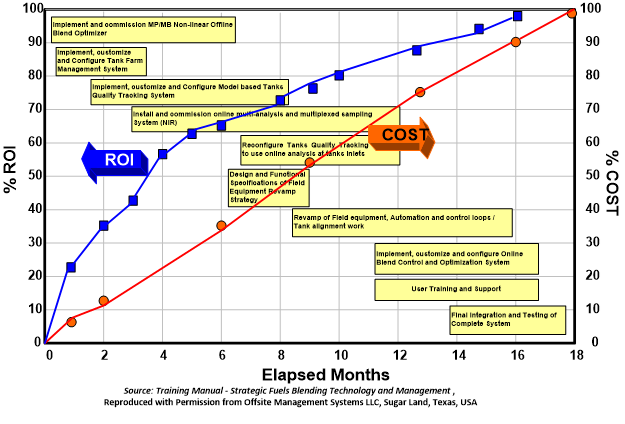
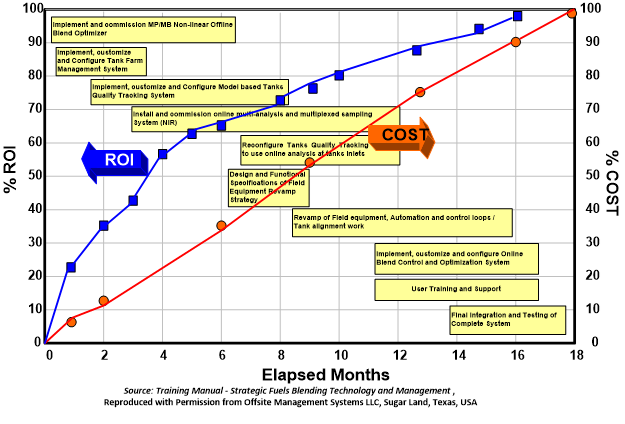
Figure 6. Return on Investment (ROI) versus Implementation for a blending project
Summary
This article has examined briefly the problems, challenges, and opportunities in a fuel blending system. The author will discuss these and more topics in a public seminar in Mumbai, India, from May 19-21, 2010 and the interested reader is encouraged to register for this seminar to learn in greater detail of the blending technology and management. The seminar details are given in this magazine issue and can also be obtained at www.globaloms.commumbai.
Bibliography
- Offsite Management Systems LLC (OMS LLC) (2009). Strategic Fuels Blending Technology and Management-Training Manual Reproduced with Permission from Offsite Management Systems LLC, Sugar Land, Texas, USA.
- Lambert, Didier (2007). Computation of Blending Indices, PTQ, Q4, pp-
- Agrawal, S. S. (2007). Advances In-Tank Quality Measurements Can Help Cut Operational Costs, Hydrocarbon Processing, 86(6), 67.
- Agrawal, S. S. (2007). Model-based Online Analysis and Monitoring of Tank Qualities, Paper presented at AICHE Spring National Meeting, April 24, 2007, Houston.
- Naughton, M. J. & Agrawal, S. S. (2007). Advanced Gasoline Blending-II, Oil & Gas Journal, 103(7), 50.
- Agrawal, S. S., & Naughton, M. J. (2007). Advanced Gasoline Blending-I, Oil & Gas Journal, 103(7), 52.
- Agrawal, S. S., Leong K.M., Wee L.H., & ECT James CTJ (2005). Implementation and Benefits of Online Tanks Quality Tracking System in a Singapore Refinery, Hydrocarbon Asia, 15(1), 36.
- Barsamian, A. (2005). Consider Near-Infrared Methods for In-line Blending: Technology and Benefits, Hydrocarbon Processing, v.84, No. 6, pp.97-100
- Barsamian, A. (2004). On-line Gasoline Blend Certification: Technology and Benefits, pp.26-37, World Refining
- Barsamian, A. (2001). Getting the Most Out of Your NIR Analyzers, Hydrocarbon Processing, v.80, No.1
- Barsamian, A. (2001). Blending Gasoline with Tier 2 Sulfur and MTBE Phase-out, ILTA 2001 International Annual Operating Conference Proceedings, Houston, Texas
- Barsamian, A. (2001). Genetic Algorithm Optimizers for Planning Applications, ISA 2001 International Conference Proceedings, Houston, Texas
- Barsamian, A. (1999). “Inline Blending Minimizes Tankage, Inventory, Giveaway, Boosts Client Satisfaction and Bottom Line”, World Refining, Nov-Dec, 1999, p.46
- Barsamian, A. and Popkowski, A. (1999). “New Gasoline Blending Unit Started at Poland Refinery” Oil & Gas Journal, July 5, p.64
- Agrawal, S. S. (1997). Advanced Closed-loop Controls of Refinery Off-site Operations, Part-II, The international Journal of Hydrocarbon Engineering, 3(4), 29
- Agrawal, S. S. (1997). Advanced Closed-loop Controls of Refinery Off-site Operations, Part-I, The international Journal of Hydrocarbon Engineering, 2(4), 28
- Agrawal, S. S., Beach, W.M., Rendon, G.T., & Olevera R.O. (1996). Implementation of Advanced on-line Blend Control, Optimization, and Planning System in Mexican Refineries, NPRA Computer Conference, Atlanta, Georgia.
- Twu, C.H. & Conn, J.E. (1996). Predict octane numbers using a generalized interaction method, Hydrocarbon Processing, 51
- Barsamian, A. and Diaz, A. (1996). Meet Changing Fuel Requirements with Online Blend Optimization, Hydrocarbon Processing, v.75, No.2, p.71
- Agrawal, S. S. (1995). Integrate blending Control, Optimization and Planning, Hydrocarbon Processing, 74(8), 129.
- Ethyl Corporation (1981). The Ethyl Technique of Octane Prediction, Report No. RTM400b
- Ethyl Corporation (1978). The Ethyl Technique Of ASTM Distillation Prediction, Report No. RTM401
- Morris, W.E. (1975). The Interaction Approach to Gasoline Blending, Presented at NPRA 73rd Annual Meeting, AM7530
- Hu, J. & Burns, A.M. (1970). New Method Predicts Cloud, Pour, Flash Points of Distillates Blends, Hydrocarbon Processing
#AdditiveBlendControls #TankGaugingSystem #LabBlendingAnalysis #MovFieldEquipment #LinearBlendModel #OnlineBlendControl #FuelsBlendingTechnology #TankQualityTracking #OfflineBlendControl #AutomationEffectivenessIndex #OperationalEfficiencyIndex #BlendingAutomationComponents #RevampBlendingProject #MinimizeQualityGiveaway
1 2 3 4 5 100%
1 2 3 4 5 0%
1 2 3 4 5 0%
1 2 3 4 5 0%
1 2 3 4 5 0%